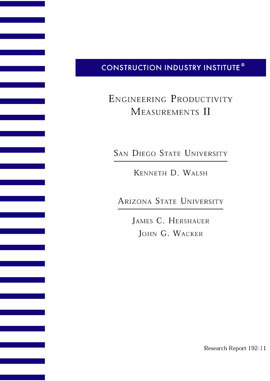
Engineering Productivity Measurements II
Although engineering generally accounts for 20 percent of total project costs, the output of the engineering team has direct bearing on the other 80 percent of project costs. For these reasons, it is important to be able to measure engineering productivity effectively. To improve productivity, there must be a good system to measure and track productivity so that the impact of productivity improvement efforts can be judged. This research provides two effective approaches to measure and track engineering productivity.
CII recognized there were no consistent standards being used throughout the industry to measure engineering productivity and commissioned the Engineering Productivity Measurements II Project Team (PT192). The objective for PT192 was to develop a standardized productivity measurement methodology and test the methodology in each of seven major disciplines.
PT192 focused on measuring engineering design hours against quantities of physical design components rather than the traditional “intermediate deliverables” such as drawings or specifications. Measuring productivity against the output of physical design components was considered to be a more consistent and reliable method and not subject to differences in work processes across the industry. Since each engineering discipline designs multiple design components, it is generally not appropriate to define output of the work of a discipline by a single design component. A method for combining quantities across several design components was developed.
An equation was developed for each discipline that uses design component quantities to calculate “basis hours.” The discipline basis hours serve as a surrogate for actual output represented in the design components. One cannot add measures of physical quantities such as cubic yards, feet, tons and numeric counts. Some method for converting quantities of a wide variety of design components to a common unit is needed. Productivity basis hours provided a common unit of measurement and a conceptual basis for developing coefficients using historical data. This was preferred over use of qualitative expert judgments of weighting factors. A productivity index for each discipline can then be calculated by dividing the actual discipline design hours by the discipline basis hours calculated from quantities of design components.
An organization needs data on a set of projects to establish a baseline. It is expected that over time the productivity index for a given organization or discipline would improve as changes are made to work processes and procedures. The research from PT192 offers two different methods to measure engineering productivity using the techniques discussed above:
- The “Off-the-Shelf” approach” uses “basis hours” equations developed from the PT192 data set to measure productivity and establish baselines. It is available in CII Implementation Resource 192-2. It can be used immediately with minimal start-up costs to monitor current and future projects. The project team collected data for 118 projects with a total installed cost of approximately $15 billion from 14 different organizations. Discipline workshops, discipline conference calls, and team discussions yielded a strong conceptual basis for which design components to include. Empirical results were used to confirm these design components and to develop models and coefficients.
- The “Custom-Tailored” approach” uses the same methodology as described in step-by-step detail in CII Research Report 192-11 to develop organization- or project-specific equations to measure or benchmark productivity. The “Custom-Tailored” approach may provide a more accurate system linked to organization-specific projects or work processes.