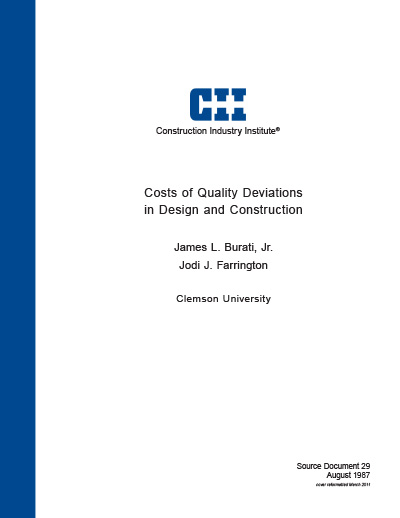
Costs of Quality Deviations in Design and Construction
Data collected from the design, construction and fabrication phases of nine industrial construction projects indicate that deviations resulting in rework (including re-design), repair or replacement accounted for an average of 12.4% of the total installed project cost. Furthermore, design changes, errors and omissions averaged 78% of the total number of deviations and 79% of the total deviation costs, while construction deviations averaged 16% of the total number of deviations and 17% of the total deviation costs.
Research Objectives
The objectives of this research study were threefold:
- to derive and present standardized definitions of quality related terminology in construction,
- to identify methods and programs of quality management currently being utilized in the construction industry, and
- to identify quality problems in construction along with their associated costs.
Research Scope
The research objectives were met through the use of surveys, questionnaires, conversations in person and by telephone, visits to home offices and construction sites, and analyses of data supplied by cooperating firms. A glossary of 25 quality-related terms was compiled to present standardized definitions that are applicable to the construction industry as a whole. A survey of QMTF member firms indicated that a wide variety of quality management systems are utilized in the construction industry. Deviation data were collected from nine fast track industrial construction projects which were completed within the last two years, each with a different designer and constructor and a TIPC of at least $5 million. The data were collected after the construction phase of the projects and identify only the costs associated with rework, repair and replacement.
Research Findings
The results of the analyses indicate that deviations on the nine projects accounted for an average of 12.4% of the TIPC. Design deviations averaged 78% of the total number of deviations, 79% of the total deviation costs and 9.5% of the TIPC, while Construction deviations averaged 16% of the total number of deviations, 17% of the total deviation costs and 2.5% of the TIPC.
Deviations relating to piping were the most frequent for the nine project averages, accounting for 25% of the total number of deviations, 24% of the total deviation costs and 3.1% of the TIPC. Mechanical deviations were the second most frequently occurring deviations, averaging 14% of the total number of deviations, 15% of the total deviation costs and 2.0% of the TIPC.
The average values obtained in this research can be considered to be valid, but conservative, indications of the areas that caused the greatest number of deviations and had the greatest cost impact for the industrial construction projects that were studied. The values are conservative because they consider the costs associated with rework, repair and replacement, but do not consider the impact costs, such as schedule impact, that might also have resulted from the deviations. Even though they are conservative, a review of the results presented in this report, along with the application to historical records of the analysis methods developed in this research effort, will help a company to identify potential problem areas on future projects.
Recommendations
- To reduce large numbers of design changes:
- firmly establish project scope
- perform constructability reviews with participation of all parties
- establish controls to limit scope modifications.
- Adopt the standard set of quality-related terminology presented in this report.
- Implement a comprehensive record-keeping system to develop an historical database necessary to identify quality problem areas.
- Utilize the historical database and the methods of analysis discussed herein to identify quality problem areas so that the number and cost of deviations can be reduced on future projects.
- Implement a quality cost tracking system to identify the costs associated with quality management as well as the costs of deviations.
- Implement a formal quality management program.