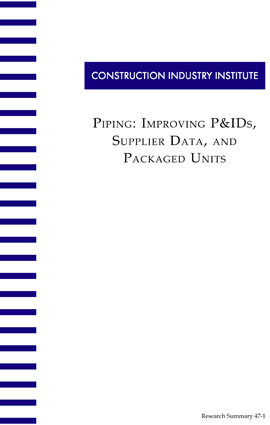
Piping: Improving P&IDs, Supplier Data, and Packaged Units
The piping function in the engineering and construction industry frequently is inefficient and problematic. Improving the piping function could amount to an average savings of $3.8 million on a $190 million heavy industrial project.
The major causes for the problem can be found in the engineering development processes for piping and instrumentation diagrams (P&IDs), supplier data, and packaged units. To address these problems, the Construction Industry Institute (CII) established the Piping Function Research Team. The team interviewed more than 100 experts from the industry to identify the drivers of the processes, to collect best practices, and to develop solution tools for improving the efficiency of the piping function.
The research team found three key drivers of P&ID problems: inefficient sequencing and prioritization, inefficient procedures for P&ID development and review, and inefficient communication of P&ID uncertainty. The team identified the major problems in the supplier data process to be communication, coordination, and selection-duration. Packaged units, according to the research team’s investigation, have problems that include issues with supplier quality and design.
To improve the efficiency of the piping function, the research team developed several tools, which are categorized into policies, procedures, and checklists. These tools have been designed so that a company, by making minor adjustments, can meet its own particular needs. This research summary provides an overview of the tools and describes the benefits that are possible when the tools are put to use
The heart of this research is to understand the drivers of late P&ID changes and to create solutions that reduce these costly changes and schedule delays. Early input can greatly improve the performance of projects in this area. To obtain this early input to P&IDs, the owner’s project team should be organized at the beginning of a project and assist in the progress of the project. In addition, lack of input by personnel from operations, maintenance and construction at the early stage of projects is also a main contributor to project uncertainty. Some companies have increased early input from these areas in order to minimize uncertainty in the piping process.
The research found that the following six stages best describe the flow of the P&ID development process (Integrated Flowchart for P&ID Development Process): (RS47-1, p. 7)
- Approval for preliminary review (AFP)
- Approval for multi-disciplinary review (AFM)
- Approval for owner review (AFO)
- Approval for detailed design (AFD)
- Approval for construction (AFC)
- Approval for start-up and operations (AFS)
To improve P&ID development and reviews, the research developed the following five tools:
- Pre-P&ID Information List
- P&ID Standardization List
- P&ID Review Checklist
- Responsibility Assignment Chart for P&ID,
- Strategies for Avoiding Artificially Frozen P&IDs
The current approach of communicating P&ID uncertainty by highlighting the uncertain area with a “cloud” and marking it with the word “hold” is inefficient. Research indicates that while the current approach is widely used, it is unsatisfactory for the following reasons (RS47-1, p. 14):
- No specific information about what is uncertain in the “hold”
- No contact point for P&ID users to clarify the information pertaining to the “hold”
- No time of reference for when the information will become firm
- No recommendation for follow-on action
Tool 1 – specifies those information items that will remain uncertain, which discipline/engineer to contact for clarifying “on-hold” information, and when “on-hold” information will be released.
Tool 2 – adds an estimated level of certainty of an “on-hold” P&ID item, and suggests a course for follow-on action.
Research has identified three major classes of problems with supplier data (RS47-1, p. 15):
- Communication problems, of which the main components are inefficiency in communicating supplier document schedules, delivery deadlines, and review schedules
- Coordination problems caused by the necessity of sharing a large amount of scattered information among various engineering disciplines
- Supplier selection problems that primarily stem from using the classical bid approach
The main cause of supplier data communication problems centers on the supplier data requests themselves. Some designers incorrectly assume that suppliers have a clear understanding of the “standard” set of drawings required to support the design effort and the information that should be included on each type of drawing. In addition, suppliers are not always fully informed as to when the designers need supplier drawings in order to support the design effort. To improve supplier data communication, a standard pre-printed form has been developed. The form should be filled out by the designer for every equipment requisition/specification issued, with commentary on its usage.
Holding regular supplier data coordination meetings is a recommended procedure for design teams. Doing so could help improve supplier data coordination.
The supplier selection process is often the primary cause for long procurement and supplier approval cycles. The cycle time to bid equipment and receive acceptable technical documentation can vary between 12 and 22 weeks, and can cause delays in producing design documents. A Supplier Pre-Qualification Program is recommended by the research team to solve this problem. (RS47-1, p. 17)
The packaged unit process is a major problem in the piping function. Research indicates that packaged unit supplier quality suffers due to:
- Insufficient supplier engineering staff
- Complexity of packaged units
- Inexperienced sub-suppliers
A Packaged Unit Supplier Pre-Qualification program should help streamline the selection process. A customization/specifications meeting between owner and designer teams prior to specification issuance is recommended. A pre-award meeting with packaged unit suppliers can also reduce packaged unit design problems. The last recommendation for reducing the packaged unit design problems is to designate the role of a packaged unit coordinator for each project. (RS47-1, p. 19)