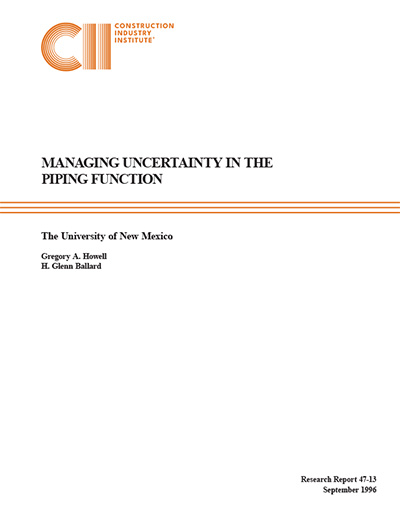
Managing Uncertainty in the Piping Process
This research reveals that:
- Deliveries of piping isometric drawings to fabricators are erratic, thus making delivery of fabricated spools to job sites equally variable.
- The most advanced project management technique for managing this uncertainty now consists of creating large inventories of pipe spools (buffers) at job sites.
- Large buffers are currently necessary for high performance. Successful projects studied in this research had at least 60 percent of all pipe on site when 20 percent of the pipe had been installed.
Seeking Flexibility Through Buffers
Experienced project managers argue forcefully that large buffers of pipe provide the flexibility to ensure uninterrupted high performance during construction. These buffers slow throughput, increase the need for working capital, lengthen construction durations, and increase on-site handling, storage and damage costs: they are an expensive cushion.
High performance not assured by buffers alone. Planning and coordination are needed to ensure that at least some of the pipe spools in the laydown yard match the valves and in-line instruments stored in the warehouse, and that some of these matched components also have pipe supports or structures to keep them in position (not to mention connecting tanks, towers or pumps). If the availability of every item is equally uncertain, very large buffers of each are needed to ensure that at least some work can proceed, and there is a very low probability that efficiency can be maximized or progress achieved in the planned sequence.
Worse, large buffers can increase uncertainty because the time spent building them reduces time available for design. In response to competitive pressure to reduce durations, many report a trend to reduce the amount of project time allowed for design. Installation begins in the field before design is stable. Incomplete drawings are either released or changed because the prerequisite documents were also incomplete. Construction planning and coordination degenerates into a struggle to find work to keep crews busy.
All this leads construction managers to push for larger buffers (and increased time available for construction) on the next job. In turn, this further reduces the time available for engineering. Thus the piping process behaves as a system where total system performance is degraded because each step is sub-optimized for the sake of flexibility.
Numerous studies have found that current project performance standards contain tremendous amounts of waste. This research suggests that a primary source of this waste can be found in the current methods of managing the flow of information and materials.
Plan Reliability: An Alternative Strategy for Managing Uncertainty
Buffers make flexibility possible. Utilizing flexibility, however, leads to an unpredictable flow of work downstream. Buffers alone cannot assure reliable production if the planning system does not produce assignments that are completed as planned.
Uncertainty cannot be eliminated by forcing premature decisions. A more effective approach is to gain control of uncertainty by making plans at each level in the planning process only to the detail supported by stable information, and finally making assignments that are certain to be completed because they are drawn from workable backlog. Workable backlog includes only those activities which have been screened to assure they are in correct sequence, adequate to maintain planned productivity, and are practical because the resources are in control. Reliable planning at every level reduces the need for buffers by assuring certainty in the flow of work. Uncertainty is not completely eliminated but its effect is limited. Reliable planning also prevents uncertainty from being injected into the flow of work by mis-application of control systems and short-term thinking. Thus the total magnitude of uncertainty is reduced, as is its downstream effect, and the need for larger buffers is reduced.
The research provided strong evidence showing that performance increases as the reliability of the planning system improves. One example: a 30 percent improvement in construction productivity occurred when planning reliability increased from 40 to 65 percent. More reliable flows provide a significant opportunity to reduce the waste associated with large buffers of pipe, and allow time and energy to improve downstream operations. Reducing the need for larger buffers means that more time is available to reduce front-end uncertainty by developing stable P&IDs or certified vendor data. Enormous opportunity exists to improve planning reliability throughout the piping process.
Last Planner: A Tool for Increasing Plan Reliability
This research offers the “Last Planner” tool, which has been proven in practice to improve planning reliability. The “Last Planner” is the person who prepares an assignment which results in immediate production work rather than providing direction for further planning. The first step is to shield through planning every worker in each function from upstream variation and uncertainty. Shielding is achieved by maintaining a backlog of workable assignments, and making assignments only from a workable backlog. Once the shield is installed, management can move upstream ahead of the shield to reduce inflow variation, and can prioritize actions based on documented causes for failure to complete planned work, to maintain a workable backlog, or to adjust activity and resource schedules to accommodate new information. Simultaneously, management can move downstream to improve performance by using techniques such as “first run studies” and in-process inspection.
From Strategy to Underlying Theory
This research reveals that two competing strategies exist for managing uncertainty in the piping process: 1) increase flexibility through the use of large buffers, and 2) increase plan reliability by making only workable assignments, thus reducing the need for buffers. Underlying these strategies are competing models of project management. The issue is one of theory and concept; how the construction process and its management are conceived. New theory makes great improvement possible because it reveals aspects of practice that have been ignored or concealed by established thinking.
One model is that of traditional project management, which focuses on individual activities that convert inputs to outputs, conceives them as contractual obligations and spends energy enforcing conformance. In this model, uncertain deliveries appear as the failure of some party to carry out their contractual duty. And since people are fallible, flexibility is required to cope with uncertainty.
The second model, the production management approach offered here, considers both activities and the flows of resources and information between them. It uses techniques to improve the reliability of those flows and relies on flexibility in proportion to uncontrolled uncertainty. Managing the rate, timing and reliability of handoffs between project participants is at the heart of production management.
When managing the piping function is reconsidered as a production management problem rather than as contract management, unreliable handoffs are understood to be the result of an unreliable planning system. Thus uncertainty can be reduced by a planning system that produces reliable assignments.