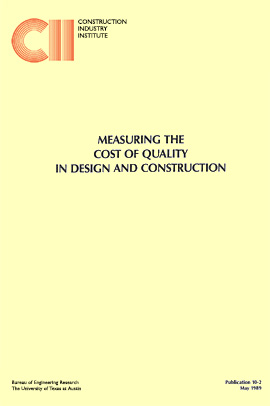
Measuring the Cost of Quality in Design and Construction
Failure to maintain quality costs the U.S. construction industry over $15 billion a year in rework expenses alone. Additional costs for other quality failures may bring the total to more than twice that amount.
Quality must be properly managed if complex industrial projects are to be completed and operated economically. How is quality managed? By controlling the costs of quality.
Defining quality in the limited and specific sense of conformance to established requirements enables the cost of quality to be measured and quantified. The goal is to minimize the cost of quality and to maximize the return on investment. Quality costs include the costs of quality management (prevention and appraisal costs) and the costs of correcting deviations. Benefits are achieved through a reduction in the costs of quality.
The Construction Industry Institute (CII) Quality Management Task Force has developed a Quality Performance Management System (QPMS) which costs little to implement. The QPMS is based on the premise that quality costs can be adequately tracked using 11 rework causes and 15 quality management activities. When categorized according to a small number of major disciplines (civil, electrical, etc.) and the major project phases (design, procurement, construction, and start-up), the resulting system is simple, flexible, cost-effective, and easily understood. The QPMS is a powerful tool for project management in terms of identifying quality issues and their impact costs, and in determining how to correct them in order to reduce project costs.
As with any tool, the QPMS requires the understanding, attention, and insight of management before it can yield the user any direct reduced costs. The QPMS allows management to place primary emphasis on those areas of greatest significance, and to understand those areas that have little or no cost consequence. Cost-tracking codes can be assigned to quality management activities and deviation rework categories, and also can be easily integrated into existing cost breakdown structure accounting systems.
The QPMS is being field-tested on eight projects. Evaluation based on early feedback indicates that the QPMS captures useful quality cost information in terms of project tasks, including quality management activities and deviation categories.
Using this streamlined, simple QPMS to track and analyze the cost of quality will boost the cost effectiveness of the construction industry on both current and future projects.
(RS10-2, p. 11)