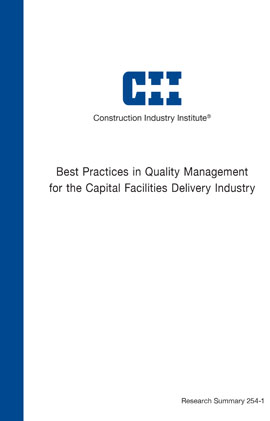
Best Practices in Quality Management for the Capital Facilities Delivery Industry
The roots of modern quality management science extend back to the early 1900s when the industrial revolution enabled the mass production of products. The ability to mass-produce drove the need to implement inspection and quality control measures in order to avoid unacceptable levels of deficiency. Beginning around 1950, a growing interest in the quality field resulted in the development of a discipline now known as quality management (QM). W. Edwards Deming, Joseph Juran, Philip Crosby, and other QM gurusmade their mark and introduced QM techniques that are still considered significant.
Today, the many challenges that confront organizations in the capital facilities delivery (CFD) industry affect the quality management systems they use. Periods of tremendous growth may be interrupted by economic downturns. Capital assets are aging, and the costs to maintain and replace them are increasing. Changing workforce demographics and the availability of resources affect the planning and execution of capital projects. These challenges intensify the need for a renewed focus on QM and on the impact that an effective quality management system (QMS) can have on the success of an organization.
Research Team 254 (RT 254) analyzed and documented the QM systems, programs, and improvement activities currently used in the CFD industry. In this process, the key elements of an effective QMS were identified as they apply to owners, contractors, and suppliers. The team found that no single QMS standard will ensure that an organization will achieve the highest levels of quality. Moreover, while ISO 9001 is the most commonly used QM standard, most of the other industry QM standards have elements in common.
RT 254 also found that organizations that reported having highly effective QM systems were differentiated by the amount of focus they placed on the following six areas:
- Leadership and management commitment to QMS
- Level of QMS training
- Emphasis on supplier and contractor QMS
- Extensive use of metrics
- Management of work process improvements
- QMS certification and accreditation.
Based on these findings, the implementation resource (IR) developed by RT 254 presents a three-step process that is supported by tools and recommendations. This resource, IR 254-2, will enable organizations to compare their present QM systems against those of organizations that report having highly effective QM systems, and to determine how best to improve them. The IR includes the following tools:
- A QM maturity matrix for the CFD industry
- Key drivers of a QMS for the CFD industry
- Comparison of the elements of QM and business excellence systems.
Prior to the industrial revolution, tradespeople were personally accountable for the quality of the products and services they provided. The members of RT 254 found it interesting that after 100 years of QM evolution, industry is returning to the concept of personal accountability. This was evidenced by the finding that organizations reporting highly effective QMS had visible and committed leadership, made extensive use of metrics, and provided training to enable employees to successfully execute tasks.
Step 1: Define and Develop Your QMS
Action #1: Understand the Requirements for a QMS
Action #2: Document the CFD Processes Governed by Your QMS
Action #3: Gain Management Commitment for QMS Implementation
Step 2: Assess the Effectiveness and Maturity of Your QMS
Action #4: Assess Your QMS Compliance with ISO 9000
Action #5: Measure QMS Effectiveness vs. Your Objectives
Action #6: Evaluate the Maturity of Your QMS
Step 3: Improve the Effectiveness of Your QMS
Action #7: Understand the Key Drivers of QMS Improvement
Action #8: Understand the Characteristics of Highly Effective QMS
Action #9: Identify and Act on QMS Improvement Opportunities