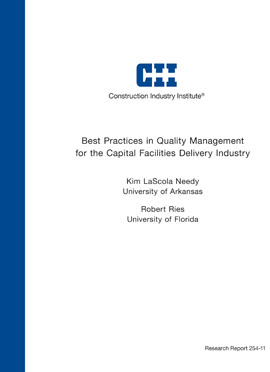
Best Practices in Quality Management for the Capital Facilities Delivery Industry
Publication No
RR254-11
Type
Academic Document
Publication Date
Jun 01, 2010
Pages
270
Research Team
RT-254
DOCUMENT DETAILS
Abstract
Filters & Tags
Abstract
Filters & Tags
Knowledge Area
Best Practice
Project Phase
Project Function
Industry Group
Research Topic
Quality Management Best Practice Refresh
Keywords
Quality,
Quality Management System,
QMS,
Quality Management Matrix,
ISO 9001,
ISO 9004,
Quality Performance Measurement,
Project Performance Measurement,
Compliance Checklist,
rt254