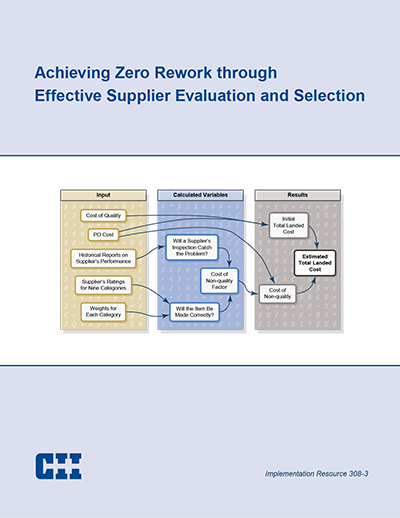
Achieving Zero Rework through Effective Supplier Evaluation and Selection
CII extended Research Team 308 (RT-308), Achieving Zero Rework through Effective Supplier Quality Practices, to answer the following essential question: How can the process and inspection capability variables be estimated for use in making estimates of the costs of non-quality in supplier selection activities? The Phase II research investigated in detail how the fabrication and inspection capabilities of suppliers are defined and how these capabilities affect the quality of the final product. The Phase II team focused on clarifying how to determine two variables:
- Pfab – the probability that the item is fabricated correctly
- Pinsp – the probability that inspection activities can catch and repair non-conformances
As part of Phase II, RT-308 identified a set of nine criteria that could be used to evaluate suppliers and could serve as a proxy to define Pfab. To its surprise, the team discovered that characteristics of prior performance were not commonly used to evaluate suppliers before new purchase order (POs) were awarded. Furthermore, companies were not collecting and/or not properly keeping important data about supplier evaluation that could be used over the long run for predictive analyses about supplier performance. Therefore, in order to more systematically collect and evaluate supplier performance data, the Phase II team built a proof-of-concept version of the Supply Chain Risk Profiler (SCRP) tool, incorporating the nine criteria used for supplier evaluations to estimate Pfab and Pinsp values for a particular supplier.
An analysis of the data RT-308 gathered during Phase II of its research revealed that a number of practices are correlated with an increase in the budgeted inspection hours for a particular PO. It also became apparent that the industry “under-plans” (or is conservative about) the inspection levels assigned to POs, and that this might be related to a misunderstanding of the factors – investigated in this project – that define suppliers’ Pfab and Pinsp capabilities. Moreover, the Phase II data suggested that several developments result under certain circumstances:
- Additional non-conformances were found when a supplier’s facility is located in a developing country.
- More inspection hours were budgeted when suppliers had low ratings in evaluations or were not evaluated.
- More non-conformances were found in the shop when a supplier’s ratings were low.