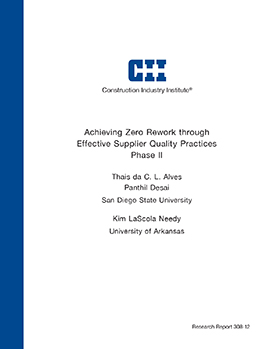
Achieving Zero Rework through Effective Supplier Quality Practices, Phase II
The original question answered by RT 308 was “What are the most effective processes and practices for ensuring that project materials and equipment are produced, manufactured, or fabricated in strict accordance with all applicable specifications, and that they are delivered to the project site without any need for rework?” The results of this effort can be found in Research Summary 308-1, Research Report 308-11, and Implementation Resource 308-2.
The project extension has investigated, in more detail, how the fabrication and inspection capability of suppliers are defined and how they impact the quality of the final product. The team decided to revisit the purchase order (PO) data collection instrument and analyze a few question of interest that had not been extensively discussed in the first phase of the project. More specifically, the team decided to take a closer look at the supplier selection process and the data provided by respondents about their practices related to supplier selection and assessment.
Furthermore, the expansion focused on further clarification of ‘how’ to determine the probability the item is fabricated correctly (Pfab) and the probability the inspection activities can catch and repair non-conformance (Pinsp). The end result, presented in the new Implementation Report 308-3, will allow for any industry, contractor, or owner/operator to easily assimilate the findings defined within IR 308-2 in ‘Estimating the Impact of the Cost of Non-quality’ on a capital project. This report addresses the additional research tasks carried out to develop the method and the beta version of the tool presented in IR308-3.
This report is structured in four main parts: Chapter 1 – Introduction, Chapter 2 – Supplier Selection and Evaluation, Chapter 3 – Analysis of Hypotheses, and Chapter 4 – Conclusions. Chapter 2 presents data on the current state of supplier evaluation and how that informed the definition of a set of supplier evaluation and selection criteria used in this project. Chapter 3 discusses results obtained from the PO instruments, used in the original project and the extension, regarding supplier evaluation and selection. Chapter 4 outlines the conclusions of this project extension and what the team accomplished.
During its Phase II research, RT-308 discovered the following impacts of supplier quality on product quality and inspection hours:
- More NCs are found when the supplier’s facility is located in a developing country.
- More inspection hours are budgeted and more NCs are found at the shop when supplier evaluation ratings are low. Additional money is spent to assure quality when these suppliers are selected.
- Subcontracting, even for portions of a commodity like shop-fabricated piping, results in budgeted more hours of inspection.
- More budgeted inspection hours are used when the supplier is NOT evaluated prior to award.