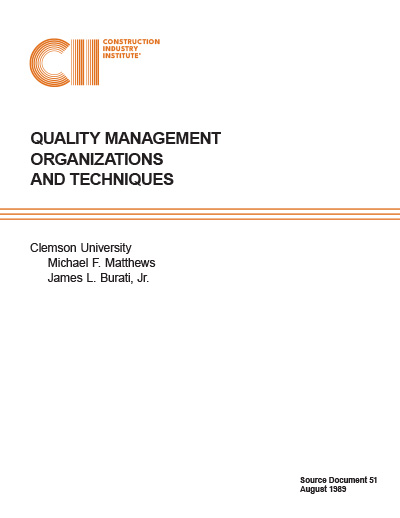
Quality Management Organizations and Techniques
Publication No
SD-51
Type
Academic Document
Publication Date
Aug 01, 1989
Pages
101
Research Team
RT-010
DOCUMENT DETAILS
Abstract
Filters & Tags
Abstract
Companies which do not implement Total Quality Management in their firms will not be competitive in the national and international market within the next 5–10 years! This startling conclusion is based on research that involved interviews with 142 individuals from 19 owner and contractor firms involved in heavy industrial, manufacturing, and commercial construction.
Total Quality Management (TQM) is a complete management philosophy that permeates every aspect of a company and places quality as a strategic issue. It is accomplished through an integrated effort between all levels of a company to increase customer satisfaction by continuously improving current performance.
Research Objectives
- Identify attributes of quality management organizations and techniques that have been considered to be effective in the construction industry.
- Identify the reasons for the effectiveness of the attributes and how they were developed and implemented.
- Recommend generic guidelines for implementing improved quality management in the construction industry.
Conclusions
- An integrated approach of Total Quality Management (TQM) and quality assurance/quality control (QA/QC) is required to provide quality products and services in the construction industry. Early indications reveal substantial improvements in achieving quality requirements among organizations that have implemented TQM.
- Construction companies have, with minor modifications, adopted the methods and concepts of TQM that are being used in U.S. manufacturing and have applied them to their operations.
- The development and deployment of a TQM approach must be tailored to the specific needs of an organization. A program can not simply be adopted from a consultant and deployed.
- There must be action behind the words and ceremony, and this can only be accomplished by senior management understanding and involvement. Management must participate in the implementation process and be fully committed to it if TQM is to succeed.
- The use of small, well-placed, pilot projects is an effective method for gaining acceptance of TQM among the employees and management of a company.
- The TQM process takes about three years before it is accepted throughout a company and significant results are achieved.
- Training for TQM will not succeed unless both the technical and humanistic aspects are addressed. The more technical the processes, the more the emphasis in training should be placed on interpersonal and communication skills.
- The topics and examples used in the training effort should be integrated with the actual work processes of the individuals being trained. The employees should apply newly learned skills to their jobs as quickly as possible.
- Statistical methods are being effectively applied to engineering and construction processes and are being used to identify and solve problems and to improve processes. For tracking to be utilized effectively, employees and management must first understand the fundamental concepts of TQM and the purpose for controlling and constantly improving their processes.
- Owners and contractors are seeking improved relationships with each other and with vendors and subcontractors. Partnership agreements are being formed between owners and contractors. Both owners and contractors are seeking to reduce their numbers of qualified vendors, but the majority feel that formal partnerships with vendors are not possible at this time.
Recommendations
- Implement an integrated approach of TQM and QA/QC.
- A TOM approach should be adapted to the specific needs of a company and not simply adopted from a consultant.
- Thoroughly investigate the different approaches to TQM and select the most applicable aspects of each one for developing a corporate approach.
- Management must fully understand and support the TQM process and actively participate in its implementation rather than delegate it.
- Use small, well-placed, pilot projects in the early stages of the deployment phase to obtain the acceptance of TQM among the employees and management of the company.
- Both the technical and humanistic aspects of TQM must be addressed by a training effort.
- Training should be tailored to the job function of the employees.
- The numbers of qualified vendors should be reduced to assist in the development of closer and more productive relationships.
Filters & Tags
Knowledge Area
Best Practice
Project Phase
Project Function
Industry Group
Research Topic
Quality Management
Keywords
quality,
quality management,
quality performance management system,
cost of quality,
cost of correcting deviations,
cost tracking,
management tool,
quantitative analysis,
rt10