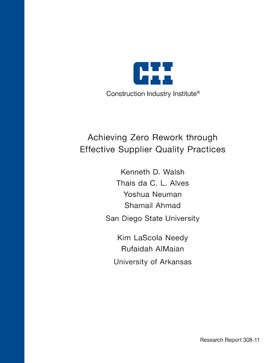
Achieving Zero Rework through Effective Supplier Quality Practices
The primary purpose of this research is to determine and substantiate the most effective processes and practices for ensuring that project materials and equipment are produced, manufactured, or fabricated in strict accordance with all applicable specifications, and that they are delivered to the project site without any need for rework. RT 308 conducted both qualitative and quantitative analyses. Qualitative methods used included interviews, the development of a team glossary, the review of literature, an analysis of documents describing or generated by supplier quality systems in use at CII member companies and their suppliers, and supplier focus groups. Quantitative methods used included the collection and analysis of data about the supplier quality practices used and outcomes achieved in actual purchases by CII member companies along with the development of a discrete-event simulation model of the function of the supplier quality system in regards to the identification and correction of non-conformances. Five objectives for the research were identified.
Objective 1: Describe how the process of assuring components are delivered to the project site at sufficient quality is performed in the construction industry, and in other industries of interest. A supplier quality process map (SQPM) comprised of five stages was developed to illustrate how the process of assuring quality from selection of supplier all the way through fabrication and mechanical completion happens. A literature review on supplier quality practices revealed that the practices used by other industries are not too different from what is being used by EPC firms, however, the consistency of use of these practices was not high in the construction sector.
Objective 2: Obtain measurements using appropriate metrics of the performance of these SQM practices, including benefit and cost parameters, to allow statistical assessment of the performance. We examined supplier quality outcomes related to the practices used to conduct quality assessments during supplier execution via a purchase order data collection instrument and a simulation model. Companies with highly effective supplier quality management systems (HECs) were studied separately to identify their specific practices. Results showed that HECs engage in more practices related to planning the inspection effort, tracking it, and periodically analyzing the process. The combination of a higher number of practices implemented by HECs across the SQPM also resulted in a higher number of NCs being found by HECs throughout the process, as well as a higher number of NCs found at the shop.
Suppliers identified practices of highly effective contractors including the use of NCRs as learning opportunities; spending more effort in planning stages; involvement of top management; use of supplier partnerships; and supplier development as effective in achieving quality. They also identified a “wish list” to improve the supplier quality process and achieve zero rework including the following practices: receive the exact specification for the product to be provided; work with standardized sets of specifications; obtain timely and positive feedback; develop upfront quality planning jointly with contractors; and engage critical resources in decision-making.
Objective 3: Develop a model for the function of the supplier quality reliability endeavor, and validate using data from existing practices. A computer simulation model was developed in EZStrobe to analyze the chance of perfect execution during the process illustrated in the SQPM using process and inspection capability as predictors. This model was later expanded to account for the cost of non-conformances in different scenarios originally envisioned by SMEs and then validated against existing data on the cost of rework available from previous studies published in the literature. Results from the simulation model indicated that the chance of achieving perfect execution is influenced more by the inspection capability as compared with the process capability.
Objective 4: Using the validated model, predict the impact of proposed practices developed by the research. A simulation model was used to study the use of inspection practices and their consistent application. It found that the outcome of the process is affected by the input parameters to varying degrees; the total costs do not vary greatly between different cost scenarios; and the effect on both the process outcome and the cost of non-conformance if the number of inspections points is reduced are significantly affected.
Objective 5: Develop appropriate deliverables for dissemination and implementation of findings to include a Research Summary, Research Report and Implementation Resource. All three publications were developed by the team and published by CII.