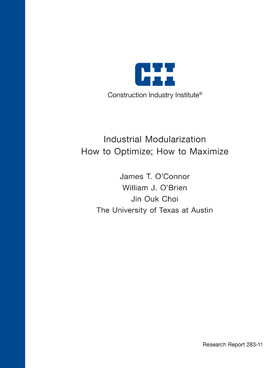
Industrial Modularization: How to Optimize; How to Maximize
The benefits from applying a modular approach to industrial projects, in contrast to a conventional stick-built approach, can vary in nature and be very significant. Yet, except in extreme conditions, the industry has been slow to achieve high levels of modularization. Some would say that the industry has hit a ceiling in terms of percent stick-built work hours being exported offsite. Research Team (RT) 283 was charged with responding to this situation through collaborative research.
In framing their purpose in the team charter, the RT stated its essential question in the following way:
What changes or adaptations in traditional project work processes are required to create an optimum environment for broader and more effective use of modularization?
Focusing on the industrial sector, the team sought to compare an idealized all-modular work process with current, largely stick-built work processes, and to identify key high-value practices that are in need of change. In addition the team sought to identify and describe both strategies and critical success factors that together can enable industry to move toward higher levels of modularization.
The team started with a review of existing modularization literature and current modularization approaches and tools used by RT member companies. From extensive review of literature, the team identified that modularization benefits are generally well recognized. These benefits include lower capital costs, improved scheduled performance, increased productivity, higher overall quality, increased safety performance, reduced waste, better environmental performance, and reduced site-based permits. Impediments or dis-benefits of modularization were also identified from the literature and these include cost barriers, engineering design barriers, procurement barriers, logistics barriers, and expertise/ culture barriers. Many ideas of how to overcome impediments were also documented from the literature review.
In-depth team discussions led to the development of five distinct solution elements: 1) Business Case process, 2) Execution Plan differences, 3) Critical success factors, 4) Standardization strategy, and 5) Modularization maximization enablers.
Regarding the first solution element, the modularization business case process should be applied at the earliest opportunity, starting as early as Opportunity Framing and analyzed in greater depth during Assessment. For the industry to truly advance, project teams would be better served by considering the modular approach to be the default approach.
Regarding the second solution element, in contrast to stick-built projects, more than 100 differences in how modular projects should be planned and executed have been identified and organized by appropriate phase of implementation. Nearly half of these are applicable during the Basic Design phase.
Regarding the third solution element, 21 high-impact Critical Success Factors (CSF) have been identified. Owner responsibilities for CSF achievement during the Assessment and Selection phases are especially significant, and the industry appears to be having particular difficulty in achieving many of the CSFs.
As described in the fourth solution element, the benefits from combining modularization with design standardization can exceed the additive sum, and therefore is deserving of special consideration. Two basic approaches exist: 1) Standard modules; and 2) Modular standardized plant (MSP). The business case for standardization should recognize ten forms of economic advantages and three forms of economic disadvantages or tradeoffs. An eight-step process has been identified for those seeking to implement the MSP strategy, and a case study provides further insight into strategy implementation.
Lastly, industry-wide barriers continue to challenge broad-based application of modularization. The fifth solution element, a listing of 10 “maximization enablers,” has been identified as recommended counter-measures to these industry-level challenges. Each element is significant in its own way and should play an important role in achieving higher levels of modularization. Thus, industry leaders and project managers should be attentive to each of these five different solution elements.