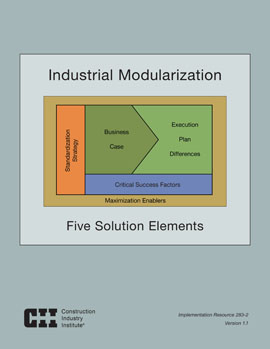
Industrial Modularization: Five Solution Elements, Version 1.1
Modularization entails the large-scale transfer of stick-build construction effort from the jobsite to one or more local or distant fabrication shops/yards, to exploit any strategic advantages. Thus, modularization may be considered a form of project business/execution strategy. While this strategy has become particularly relevant to the industrial sector of the capital projects industry over the last 25 years, industrial projects are still in need of detailed guidance on when and how to more effectively exploit modularization. While modularization benefits can vary in nature and be very significant, industry has been slow to achieve higher levels of modularization, except under extreme conditions. Some would say that the industry has hit a ceiling in terms of percentage of stick-build work hours being exported to fabrication shops and yards.
CII Research Team (RT) 283 was charged with responding to this situation through collaborative research. In framing its purpose in the team charter, the RT formulated its essential question in the following way:
Which changes or adaptations in traditional project work processes are necessary to creating an optimal environment for broader and more effective use of modularization?
The reader should recognize that the research team and this research product are not focused on promoting or marketing the concept of modularization, but rather on helping project teams better understand whether modularization is the right strategy for the project—and if so, how to be most successful at implementing the strategy.
To identify key high-value practices in need of change or adaptation to project work processes, the team sought to compare an idealized all-modular work process with current, largely stick-build work processes. In addition, the team sought to isolate and characterize related critical success factors, and to identify and describe industry-level strategies that, when deployed with a focus on the critical success factors, can help the industry move toward higher levels of modularization.
While many research findings may apply equally well to the commercial and infrastructure project sectors, the scope of the study was limited primarily to the industrial sub-sector. This area of the market includes process and manufacturing facilities such as offshore facilities, petrochemical plants, power plants, and pharmaceutical plants, among others. Moreover, in contrast to the narrower charge originally given to the research team from the CII Research Committee, the study scope was deliberately broadened to include issues and opportunities related to front end planning and equipment manufacturing.
At the outset, to ensure its internal alignment and establish a foundation for subsequent developments, the team needed to clarify its terminology. Following are two key terms the team defined precisely:
- Module: Portion of plant fully fabricated, assembled, and tested away from the final site placement, in so far as is practical.
- % Modularization: Portion of original site-based work hours (excluding site preparation and demolition) exported to fabrication shops.
This research led to the development of five distinct solution elements: 1) business case process, 2) execution plan differences, 3) critical success factors (CSFs), 4) standardization strategy, and 5) modularization maximization enablers.
Is the standard procedure for adopting the business case process for Modularization. (Supports Key Finding 1)
IR283-2, Module Standardized Plant (MSP)
8 Step Process to integrate design standardization and modularization. (Supports Key Finding 4)