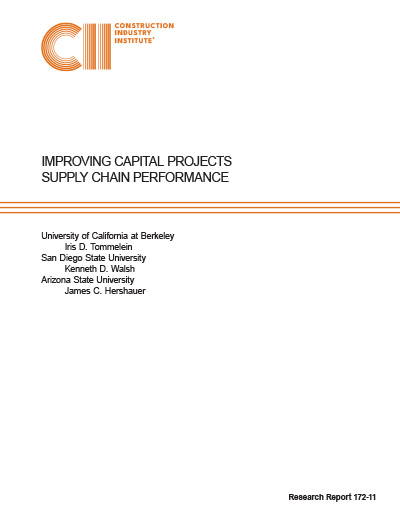
Improving Capital Projects Supply Chain Performance
Supply Chain Management (SCM) is recognized as a leading process improvement, cost saving, and revenue-enhancing business strategy. It applies to all businesses involved in the delivery of capital projects. SCM requires a corporate initiative, supported by strategic and tactical planning, to instill systems thinking and promote a new discipline that companies must master.
Examples of capital projects SCM (CPs SCM) tools and techniques are presented in this document. CPs SCM requires a good understanding of production management; planning, design, and construction; and business drivers. Like other disciplines within an organization, such as structural, mechanical, electrical, or process engineering, accounting, and materials management, SCM must have a champion who can drive the ideas across disciplines within the organization as well as across organizational boundaries.
SCM may be practiced on a single project, but it results in the greatest benefits when it is practiced at the enterprise level, when it involves multiple companies, and when it gets applied to multiple projects over an extended period of time. Successful application of SCM to the delivery of capital projects therefore requires a major shift in mindset from all participants involved in the delivery of capital projects. Companies not engaging in SCM may find themselves falling rapidly behind in performance relative to their supply-chain conscious competitors.
Managing a supply chain is challenging. It requires adopting a global systems perspective, rather than the traditional, often shortsighted view of a single stakeholder. In the construction industry, traditional managerial approaches emphasize: management of individual projects; separation of design, installation, and operation functions; uniquely engineered facilities and components; competitive bidding; early delivery of all materials at construction sites; and information hoarding. These practices characteristically fail to capture the advantages of synergies and leverage that may be obtained by taking a multi-project perspective.
With the application of SCM to the delivery of capital projects, managerial approaches will emphasize: supply-based management; life-cycle costing; assembly of unique facilities from standardized modules and components; problem solving through strategic partnering; emphasis on long-term working relationships; extensive use of communication and information technology so that the value chain supports the supply chain; short and reliable cycle times from raw materials to site (and/or strategic placement of inventory in critical material supply chains); phased delivery of materials to the construction site to match installation rates; and information visibility that allows efficiencies such as risk pooling, logistics optimization, and Supplier Managed Inventory.
Industry leaders will effectively manage their supply chains and thereby gain significant competitive advantage. All key stakeholders in the construction supply chain must understand the opportunities offered by SCM and jointly take advantage of them, or those left behind will be unable to compete in the long term.
It is necessary to optimize supply chain leadership through strategic innovation and alignment. Existing boundaries of firms need to become relatively porous and flexible. Capital projects markets require a focus on building collaboration in relationships within and across key and often multiple industry players.
Application of supply chain concepts and practices in the construction industry—the industry that delivers capital projects—can lead to improvements in the following areas:
Cost |
|
Time |
|
Quality |
|
Safety |
|
Case Study 1 illustrates the benefits of forming preferred supplier relationship with key suppliers. The buying organization in this case study was able to achieve the following goals by initiating a preferred supplier relationship: (RR172-11, p. 27)
- Reduce non-value adding activities (Table 3.3 below)
- Assure only owner-approved materials are supplied
- Implement Just-in-Time (JIT) deliveries through greater flexibility in warehousing, expedited delivery and access to inventory
- Reduce internal overhead cost
- Reduce total cost to the owner