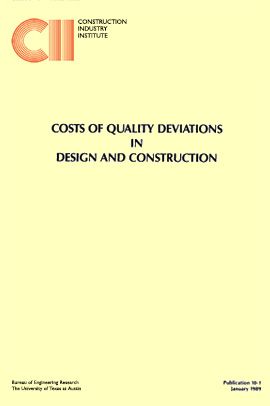
Costs of Quality Deviations in Design and Construction
The average cost of rework on industrial projects exceeds 12 percent. For the $140 billion U.S. construction industry, this means that we waste in excess of $17 billion annually. These costs can be significantly reduced through better quality management. Design deviations (changes, errors, and omissions) accounted for roughly 80 percent of the increased costs, while construction deviations accounted for only about 20 percent. A Quality Performance Management System (QPMS) has been developed (Appendix E) that can be used as a management tool to identify and reduce deviation costs.
Objective of Study
The objective of the Quality Management Task Force study was to identify and quantify the magnitude of rework costs resulting from quality deviations in design and construction, and to present data that will encourage the construction industry to implement systems such as the QPMS to reduce these costs.
Recommendations
- Reduce the number of design changes by:
- establishing definitive project scope.
- performing periodic reviews with participation of all parties.
- establishing procedures to limit scope modifications.
- Implement a quality management program that has total commitment at all levels in the firm.
- Adopt the standard set of quality-related terminology presented in Appendix A.
- Develop and implement a system to establish a database necessary to identify deviation costs and quality problem areas.
- Implement a Quality Performance Management System.
Is a management tool providing for the quantitative analysis of certain quality-related aspects of design and construction by systematically collecting and classifying the costs of quality. The cost of quality is defined as the cost of correcting deviations (rework) plus the cost of quality management activities. (RS10-1, p. 23)