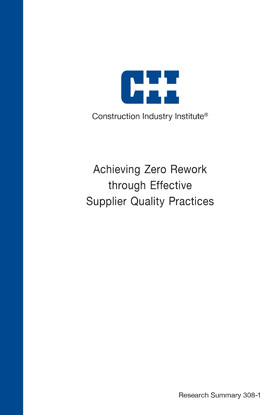
Achieving Zero Rework through Effective Supplier Quality Practices
The quality of materials and equipment supplied to a capital project directly affects the ability of the project team to complete it on time and on budget. The fact that so many items are custom, one-of-a-kind, or made of rare materials makes supplier quality particularly important in the construction of capital projects. CII Research Team (RT) 308, Achieving Zero Rework through Effective Supplier Quality Practices, worked to find the most effective processes and practices for ensuring that project materials and equipment are produced, manufactured, or fabricated in strict accordance with all applicable specifications and that, once delivered to the project site, they do not require any rework.
The research team pursued the following objectives:
- Describe the current processes for assuring component quality in the construction industry and other industries of interest.
- Measure the performance of these practices with appropriate metrics.
- Develop and validate a model of the supplier quality reliability endeavor.
- Use the model developed to propose alternative practices, and predict the impact of these new practices.
- Develop appropriate vehicles for dissemination and implementation of the findings.
The team gathered the data for this research from the following sources: documents from owner, contractor, and supplier companies; research literature on quality in construction and other industries; interviews at contractor and supplier facilities; supplier focus groups; CII member purchase order records. Using this data, the research team developed the following: the Supplier Quality Process Map; a summary of current practices found in the literature; a glossary of terms and acronyms; a supplier wish list of purchaser practices; statistical analysis of current supplier quality surveillance (SQS) performance for several commodity categories; and a simulation model for estimating the impact of the cost of non-quality to support supplier selection.
While the review of literature outside the industry did not find any work processes that are not already used in construction, the team did discover that these practices are not applied consistently across the industry. In addition, the literature review and simulation model do not support the commonly held notion that inspection is not an effective method of improving manufacturing quality outcomes. Based on its findings, RT 308 recommends that companies consistently use the practices presented in Implementation Resource (IR) 308-2, Achieving Zero Rework through Effective Supplier Quality Practices, to manage supplier quality. The team further encourages readers to utilize the decision-support tool also presented in that resource, to project the cost of non-quality and to support supplier selection.
RT-308’s Phase II researchers developed a method of applying indicators and reports commonly used in the industry to develop calculations (e.g., corrective action reports, preventive action reports, and non-conformance reports), as well as repurposing the nine criteria used for supplier evaluations to estimate values for Pfab and Pinsp for a particular supplier. The team tested its resulting Supply Chain Risk Profiler tool mostly by using data collected from the PO instrument and conferring with subject matter experts within the CII community.
The team also developed a glossary of terms and definitions related to the Supply Chain Risk Profiler tool to expand efforts to define a common language that could be used in the process of selecting and evaluating suppliers, and during the supplier quality surveillance (SQS) function:
- Cost of Non-quality (CostNQ)
- Total Landed Cost including the Cost of Non-quality (TLC+NQ)
- Number of non-conformances – used as a proxy for quality
- Pfab – fabrication capability, calculated using supplier ratings
- Pinsp – inspection capability, calculated using quality-related data (number of non-conformances, corrective action reports, and preventive action reports)