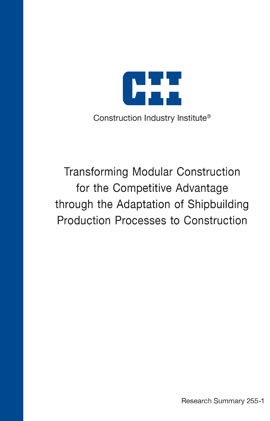
Transforming Modular Construction for the Competitive Advantage through the Adaptation of Shipbuildi
Building on the work of CII Research Team 232 on the potential for adapting shipbuilding techniques to construction, Research Team 255 focused on evaluating the potential of the shipbuilding industry’s Interim Product Database process (IPD) approach for use in the construction industry. Simply defined, the IPD process incorporates scalable, pre-designed blocks or modules, consisting of hierarchical interim subassemblies and stored in an all-encompassing database.
RT 232 noted in 2006 that the global shipbuilding industry had undergone a transformation over the previous two decades, a shift that brought about dramatic reductions in cost and construction cycle times. In essence, the industry transformed itself from one that made traditional one-off, stick-built constructed products to one that utilizes modularization, automation, design reuse through product families and interim products, along with extensive supply-chain integration. The result of these changes has been the industry’s ability to deliver products faster, at lower cost, while still maintaining both quality and safety standards. RT 232 also postulated that this development of reusable, scalable modular product-family designs and interim products—referred to as the Interim Product Database—held significant potential for use in the construction industry.
RT 255 focused its efforts on identifying examples of construction projects that had incorporated one or more aspects of the IPD process and that had moved beyond the standard one-off modular construction approach. This effort involved conducting case studies from a broad cross-section of construction projects that included pharmaceutical (manufacturing and R&D), petrochemical, residential, office, hospitality, and civil works (dams and bridges). The team’s subsequent review and findings included the following:
- Significant use of modular construction is occurring across many sectors of the industry, with pockets of enhanced modular execution. This increased use of modularization is mostly driven by owners’ needs for faster project delivery.
- Significant schedule compression is being achieved.
- Limited hard cost savings can be attributed to not using manufacturing techniques and limited reuse of design. However, soft costs savings associated with such areas as quality, safety, site congestion, and workforce stability, were not typically included in the cost-benefit analysis due to quantification challenges.
- Single-project focus with rare exceptions.
- Improved safety and reduced site congestion are a result of increased modularization.
- Implementation barriers include re-thinking the planning/design process, module size, transportation, code compliance, design scalability/repeatability, customization, and initial investment costs versus long payback.
RT 255 also concluded that there are sufficient data to suggest that the IPD process can generate for the construction industry the same kind of transformation it has effected in the shipbuilding industry. Following are the areas that stand to be improved:
- Shorter schedule – The actual time to deliver the constructed facility is significantly reduced. Today’s business environment drives many owners to complete construction projects as quickly as possible, so that plants can get their product to market sooner.
- Lower material costs – Standardized sub-assembly materials can be purchased in bulk, reducing material costs through economies of scale and optimization of the supply chain.
- Higher quality – The controlled environment and standard module design associated with a manufacturing-type scenario eliminates inclement weather, site access, height constraints, and skilled labor. They also allow for more thorough QA checks and inspection.
- Innovation improvements – The manufacturing-type environment facilitates the introduction of labor-saving techniques (e.g., the use of jigs, automation, and robotics) to optimize production at lower cost.
- Reduce design time – The development of a qualified design library allows for the adaptive reuse of standardized designs, resulting a reduced design completion schedule.
- Safer construction – The manufacturing-type environment can facilitate a safer construction environment and reduce hazards associated with field installation.
This has been identified as the number one benefit for adopting IPD modular construction techniques. Modular construction is occurring based on the IPD shipbuilding model with execution driven mostly by owners’ needs for faster project delivery. Case studies (listed in Table 1 in RS255-1) have shown that significant schedule compression is being achieved. The IPD methodology currently generates a substantial reduction in the engineering design time for ships – up to 80 percent. This savings on design is largely realized from the adaptive reuse of a standing database library of qualified and scalable designs, with very limited new design.
- Five case studies identified schedule improvements between 15 - 50% over original baseline schedules due to the modular approach that allows for paralleling activities, construction out of season.
- Cost savings were marginal or non-existent.
Case studies have shown various implementation barriers exist to successfully execute a project based on the IPD model. RT-255 identified 22 barriers grouped into the following six categories. (Reference RS255-1 Appendix, page 35 for a detailed construction methodology barrier analysis.)
- Execution considerations (4)
- Integration for reusable modular construction
- Customization
- Ability to scale and repeatability
- Plant capability
- Design considerations (4)
- Natural phenomena
- Site constraints
- Codes and standards
- Inspection and tests
- Transportation considerations (5)
- Travel distance and cost
- Road restrictions
- Handling capabilities
- Shipping and packaging
- Transportation risks
- Module interface considerations (2)
- Interface tolerances
- Ability to handle field changes
- Labor considerations (3)
- Labor at construction site
- Labor at fabrication area
- Labor agreement
- Long-term methodology considerations (4)
- Market size
- Initial funding
- Long term funding
- Regulations and codes