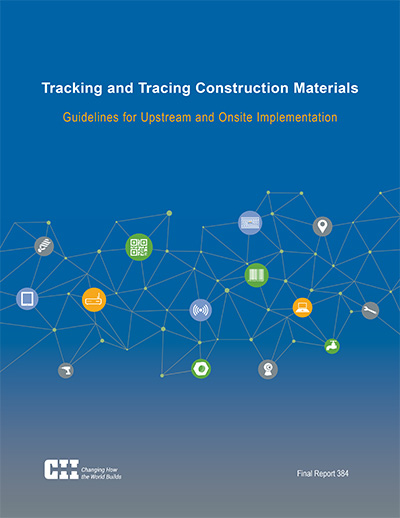
Tracking and Tracing Construction Materials: Guidelines for Upstream and Onsite Implementation
The ability to track and trace upstream materials allows vendors and suppliers to seamlessly share production status and other materials information with key project stakeholders. These updates promise to greatly improve supply chain visibility and construction efficiency, and thereby to positively affect craft labor productivity, cost, and time.
RT-384 arrived at the following key findings:
- Tracing the Digital Information Thread Offers a Novel Opportunity – Like two sides of the same coin, tracking and tracing should be regarded as two complementary and fundamental aspects of a digital materials function. However, construction professionals rarely leverage the ability to trace data about a component from its production to its current status and share that information with key project stakeholders. RT-384 found anecdotal evidence that tracing and sharing the digital information thread of a component (e.g., certification, vendor data, configuration, subcomponent details, and maintenance records) can assist receiving, installation, commissioning and startup, and operations and maintenance. Traceability of information becomes especially important for components that belong to the owner’s operation process, such as complex equipment packages or modules.
- Perceptions of a Questionable Return on Investment and How to Mitigate Them – The perception of a poor return on investment (ROI) stands as a major barrier to the adoption of tracking and tracing by owner, contractor, vendor, and supplier organizations alike. This negative perception contrasts with the experience of SMEs who, during interviews with RT-384, emphasized that, when properly planned and implemented, the digital information thread often provides an ROI of multiple times the investment costs.
- Costs vs. Benefits – Implementation of tracking and tracing requires an upfront investment in information technologies and work process alignment. Thus, stakeholders who explore the use of tracking and tracing often seek to understand the cost-to-benefit in order to justify such an investment. In order to provide clarity, RT-384 documented four construction functions that saw a direct cost-benefit from tracking and tracing:
- Automated material transactions
- Onsite material searches
- Craft labor productivity
- Construction operations, which benefit from planning reliability when fed upstream and onsite materials updates and information
The team also found anecdotal evidence that documenting and sharing materials information at vendors and suppliers could discourage legal actions among key stakeholders. Indeed, two construction organizations that contributed to this research mentioned that this legal mitigation aspect had become the main driver for their adoption of upstream tracking.
Finally, the ability to seamlessly trace and access materials’ data on production, testing, certifications, installation, and design holds the promise to significantly simplify information management and reduce the amount of time devoted to typing and accessing this information.
- A Digital Materials Model – A digital materials model emerged from the team’s analysis of SME interviews on project experiences with outstanding materials tracking and tracing functions both upstream and onsite. During the analysis, common themes emerged that enabled the team to define 43 strategies. RT-384 grouped these strategies into 10 functions, which spanned four sequential implementation stages: consultation, requests for proposals, upstream tracking and tracing, and onsite tracking and tracing.
- The Relative Importance of Strategies – RT-384 dedicated a workshop to weighting the 43 strategies in the model with input from SMEs. In this system, a higher weight indicates a higher contribution to the maturity of the materials tracking and tracing function, and, consequently, to project performance. The sum of weights gives a model user both maturity scores by function and stage, and the ability to compare them.
- Maturity Assessment Tool and Score – The research team developed a computer-based tool that evaluates digital materials’ readiness against the digital materials model. This tool leverages the model and relative weights to compute a unified maturity score for a project. Alternatively, the tool can evaluate the maturity of one or more implementation stages independently. The tool generates a report that identifies leverage areas and corresponding actions to enhance the maturity of tracking and tracing.
- Tracking and Tracing Subcomponents – Whenever complex components (e.g., pumps, turbines, compressors), packages, or construction modules are to be digitally tracked, their subcomponents must also be tracked. A logical relationship must be established among tracking devices that replicates the dependency between components and subcomponents, for example, through parent-child or one-to-many relationships. Such dependency is often replicated in the selection of tracking technology devices, for instance, by dedicating more expensive resources to the tracking of the main component(s).
- Potential Impact on the Entire Project Life-cycle – RT-384’s analysis of both surveys and interviews highlighted the potential of materials tracking and tracing to improve the entire life-cycle of a project. SMEs indicated the positive effects on commissioning and startup and operations and maintenance when a project shared a digital thread of information for every component. For example, the research team collected anecdotal evidence of projects that substantially reduced commissioning and startup completion times by making such digital information available at the fingertips of the commissioning team through portable electronic devices.
Like two sides of the same coin, tracking and tracing should be regarded as two complementary and fundamental aspects of a digital materials function. Construction professionals have mostly limited their practice to tracking the status and location of material components on the site – tracing and sharing the information of a component spanning back to its production is rarely leveraged. RT-384 found anecdotal evidence that tracing and sharing the full digital information thread of a component can positively affect receiving, installation, commissioning and startup, and operations and maintenance (FR-384, p. 2).
Upstream tracking and tracing (“upstream tracking” in brief) aims at proactively communicating production, shipment, and delivery information and updates from vendors and suppliers to project stakeholders. It also encompasses communicating warnings when issues arise, such as fabrication delays. RT-384 defines upstream tracking as, “the capture, communication, and sharing of material status and information from vendors and suppliers to the project team” (FR-384, p. 1).
The research team surveyed industry practitioners to identify the barriers to and enablers of upstream tracking:
Top Barriers:
|
Top Enablers:
|
The survey found that the perception of upstream tracking as a questionable investment is a major standing barrier for owner, contractor, and vendor and supplier organizations alike (see Figure 1) (FR-384, p. 19).
Figure 1. Difficulty to Predict a Clear ROI for Adopting Upstream Tracking
SMEs interviewed by the research team emphasized the benefits of tracking and tracing. When properly planned and implemented, upstream tracking often provides an ROI of multiple times the investment costs. In order to alleviate the negative perceptions, the SMEs recommended meeting with hesitant project teams and managers to resolve their questions and walk them through the implementation steps. In order to provide clarity, RT-384 documented four construction functions with evidence of a direct cost-benefit from tracking and tracking: automated material transactions, onsite material searches, craft labor productivity, and construction operations.
A digital materials model emerged from the team’s analysis of SME interviews on project experiences with remarkable materials tracking and tracing functions both upstream and onsite. During the analysis, common themes emerged and led to the definition of 43 strategies. The strategies are grouped into 10 functions, which at the same time are divided into four sequential implementation stages: consultation, requests for proposals, upstream tracking and tracing, and onsite tracking and tracing (see Figure 2). With input from SMEs, the team weighted these strategies (FR-384, p. 7).
Figure 2. Digital Materials Model
- Level 1 or very poor – major deficiencies
- Level 2 or poor – moderate deficiencies
- Level 3 or good – minor deficiencies
- Level 4 or very good – complete (or nearly complete) implementation
Figure 3. Maturity Level Definitions from the Digital Materials Model
RT-384 intended for these definitions to guide industry organizations in their tracking and tracing journey, regardless of their level of knowledge and expertise, and to drive the model’s progressive implementation.
Figure 5. Maturity Report from the Digital Materials Model