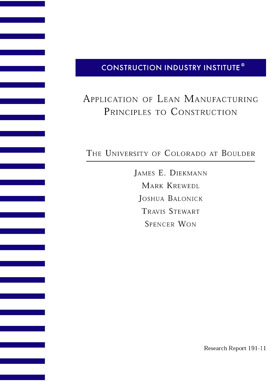
Application of Lean Manufacturing Principles to Construction
Over the past three decades, the U.S. construction industry has seen a decline in both its share of the gross national product and its annual productivity growth rate. The quality of construction has faltered during this period as well. In contrast, the U.S. manufacturing industry has made significant progress in increasing productivity and product quality while lowering product lead times. Manufacturing has essentially made the transition from second class to world class.
The improvements in manufacturing processes have included reducing the amount of human effort, space and inventory required in the factory and increasing the quality and variety of products and the flexibility of manufacturing operations. The application of “lean production” principles to manufacturing processes has been instrumental in achieving these results. Lean principles were developed in post–World War II Japan at the Toyota Motor Company. These principles evolved from geographic and economic constraints, from top-down, management-led innovation and from bottom-up pragmatic problem solving. They became collectively known as the Toyota Production System (Womack et al. 1990).
The principles of lean theory are conceptualized at the process, project and enterprise or organization levels. Various principles, methods, and tools can be applied at each level, so that lean production becomes an inclusive philosophy aimed at continuously improving the entire production organization as well as the physical production process.
If manufacturing can make such vast improvements in quality and productivity, while reducing costs and lead times, why not construction? This report identifies the core principles of lean production, compares and contrasts the manufacturing and construction industries, and identifies the potential for implementing lean principles in the construction industry.
The research team started with the following definition of lean construction:
Lean construction is the continuous process of eliminating waste, meeting or exceeding all customer requirements, focusing on the entire value stream, and pursuing perfection in the execution of a constructed project.
This definition includes many fundamental aspects of a lean philosophy. It is a philosophy that requires a continuous improvement effort that is focused on a value stream defined in terms of the needs of the customer. Improvement is, in part, accomplished by eliminating waste in the process.
Lean philosophy, broadly defined, can apply to design, procurement and production functions. To help define and direct research efforts and to present an elemental contribution to understanding lean principles in construction, the scope of this report was limited primarily to construction field operations. Although the focus of the inquiry was field operations, researchers were sensitive to the effects of policy and actions that occur at the enterprise, project and process levels. Two considerations led the research team to focus primary attention on construction field operations. First, field operations are where most of the value is added from the customer’s point of view. Cognizance of customer value is central to a lean philosophy. Second, other researchers have studied value streams and other aspects of lean philosophy.
From this basis, the following questions were developed:
- Are lean principles as defined in manufacturing applicable to the construction industry? If not, are there other principles that are more appropriate for construction?
- What is the nature of the typical construction production value stream?
- How should conformance to lean principles be measured?
- Are lean principles commonly used in the construction industry?
- What is the path forward to becoming lean?
- What are the roadblocks to adopting a lean culture?
These questions were investigated using a multifaceted approach. First, lean literature was examined from manufacturing, construction and other industries such as shipbuilding, aerospace, and software engineering. Second, advice from lean manufacturing pioneers was used, and the construction production value stream was studied. Next, contractors (both lean and non-lean) were surveyed to learn about lean practices that are currently employed in the construction industry.
Using all of this information, a set of lean principles was developed that is appropriate for construction. In general, it can be concluded that construction owners and contractors would significantly benefit from the adoption of lean principles and behaviors. The value added portion of the typical field construction value stream is exceedingly small, comprising approximately 10 percent of all crew level activities. It was determined that lean behavior among construction contractors is rare, even with contractors who are actively pursuing the lean ideal, because being truly lean requires changes to every aspect and level of a company. Additionally, becoming a lean contractor is difficult in part because of the dynamic nature of construction, but mostly because construction contractors control such a small portion of the construction value stream.
For those wishing to start the lean journey in their company, a lean workplace can be created using the following steps:
- Identify waste in field operations.
- Drive out waste.
- Standardize the workplace.
- Develop a lean culture.
- Involve the client.
- Continuously improve.
Becoming lean is a long-term, comprehensive commitment; it amounts to a cultural change for the company. Construction is no simple deterministic system. Lean principles must be understood and applied in a context and require a comprehensive understanding of a complex, interacting and uncertain construction system. Many lean principles can be understood as attempts to increase preplanning ability, improve organizational design and increase flexibility.
In this light, the final conclusion is that lean cannot be reduced to a set of rules or tools. It must be approached as a system of thinking and behavior that is shared throughout the value stream. Given that contractors control such a small portion of the construction value stream (as compared to their manufacturing counterparts), this is the challenge that faces the potential lean contractor. If successfully applied, however, lean has the potential to improve the cost structure, value attitudes and delivery times of the construction industry.