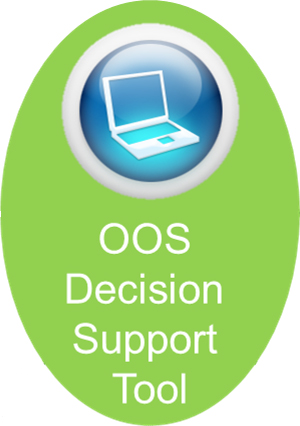
The Out-of-Sequence Decision Support System
RT-334 identified 88 causes and 56 warning signs of OOS, spanning 11 categories, as shown in Figure 2.
Figure 2. Numbers of Identified OOS Cause and Warning Signs Spanning the Studied Categories
Through its expert-based study, RT-334 established the likelihood of occurrence and relative impact of these 88 OOS causes, and used this information to calculate corresponding risk ratings for each cause. These risk ratings were then used to categorize the causes into six risk tiers, with risk-tier 1 being the riskiest and risk-tier 6 being least risky. Following are the first two risk-tiers, including the top 10 causes of OOS:
Risk-tier 1: | Category: | |
1. Late design deliverables | Engineering | |
2. Changes in design | Engineering | |
3. Expedited schedule to meet owner’s requirements | Execution | |
Risk-tier 2: |
||
4. Schedule pressure | Execution | |
5. Late vendor information | Engineering | |
6. Late delivery from vendors | Materials management | |
7. Unrealistic activities duration | Planning | |
8. Poor communication between project parties | Project team | |
9. Late scope changes requiring different equipment/processes | Change management | |
10. Low clarity of scope | Planning |
In addition, statistical tests were performed to reveal the statistically significant different perspectives that owners and contractors have regarding the causes of OOS. At a 5% statistical significance level, it was shown that owners rated the likelihood of occurrent of two causes higher than contractors, and that contractors rated the relative impact of 10 causes higher than owners.
Also, the strength of correlation between the 56 identified warning signs and the occurrence of OOS was determined through the expert-based study, and used to rank the warning signs from most accurate to least accurate in anticipating that OOS is about to happen. Following are the top five warning signs of OOS:
Top Five Warning Signs of OOS: | Category: | |
1. Late start of pre-commissioning activities | Commissioning | |
2. Low wages relative to close by projects | Resource management | |
3. Growing percentage of critical activities in schedule | Execution | |
4. Inadequate quality management personnel on site | Quality management | |
5. Late purchase orders | Materials management |
All reported findings regarding OOS causes and warning signs were validated by the 42 projects the team tracked through the project-based study. Furthermore, the project-based study demonstrated that the projects that experience significant OOS differ from the projects that succeed in minimizing OOS in five team-related factors, four planning-related factors, two project-related factors, and six execution-related factors.
The projects RT-334 tracked in the project-based study demonstrate that on average:
- 15% of total project activities are performed as OOS
- This OOS work results, on average, in the following consequences:
- 33% increase in construction schedule
- 25% increase in construction cost
Furthermore, 26% of the studied projects reported that they spent more than 25% of their construction cost on OOS. Also, 29% of the studied projects reported that they spent more than 25% of their hours performing OOS.
In addition, the experts RT-334 surveyed in the study highly rated the negative impacts of OOS on schedule, productivity, cost, quality, and safety. For example, 85% of the experts reported that OOS causes significant to extreme schedule overrun; 74% reported that OOS causes significant to extreme productivity loss; and 73% reported that OOS causes significant to extreme cost overruns.
Furthermore, the relationship between OOS and 12 lagging performance indicators, spanning five performance areas (i.e., schedule, productivity, cost, quality, and safety), was statistically tested through the project-based study. At 95% statistical confidence level, it was shown that OOS results in:
- Cost growth
- Lower productivity index (earned/actual)
- Higher project hours factor
- Schedule growth
- Higher project schedule factor
- Higher rework percentage
- Higher number of drawing revisions
- Higher number of non-conformity reports
- Higher value of punch-list items
For example, Figure 3 shows the statistically significant inverse relationship between OOS and productivity index, indicating that as the percentage of hours spent on OOS increases, the project productivity index significantly decreases.
Figure 3. Inverse Relationship between OOS and Productivity Index (Earned/Actual)
Statistical analysis of the projects RT-334 tracked through the study showed that a 5% increase in OOS causes, on average, the following consequences:
- 10% increase in construction cost
- 8.5% drop in labor productivity
- 11% increase in construction schedule
- 5% increase in rework