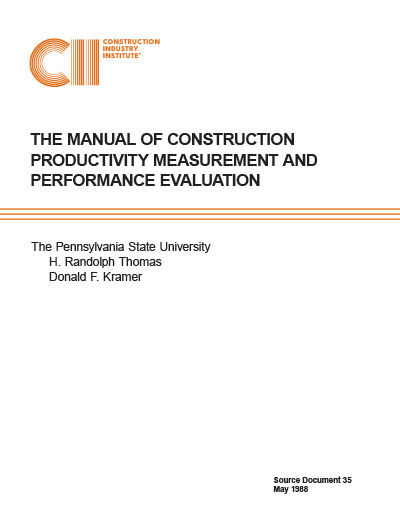
The Manual of Construction Productivity Measurement and Performance Evaluation
In 1968, representatives from a number of major U.S. corporations joined to form the Construction Roundtable. The catalyst that led to the creation of this group was their concern over the increased cost of construction. The inflation rate was rising to record levels, and there had been a noticeable decline in construction productivity.
Construction Users Anti-Inflation Roundtable, later known as the Business Roundtable, was formed in 1972 to promote discussions and action on a wide range of public issues affecting major corporations. The Construction Roundtable was absorbed by this organization. Over the years, the Roundtable has been concerned with the quality, efficiency, productivity, and effectiveness of the construction industry. In particular, the Roundtable’s Construction Industry Cost Effectiveness (CICE) Project, conceived in 1977, looked at specific problem areas in the construction industry.
The CICE Project produced 23 detailed reports. One of these was Report A-1 titled, “Measuring Productivity in Construction.” This study found that there is no common definition of construction productivity. Even when definitions are consistent, approaches to measuring input and output vary so greatly that valid comparisons between projects are almost impossible. Furthermore there is a need for better measurement approaches that apply more specifically to the work at the task level. The report recognized the importance of productivity measurement for determining trends and levels of productivity and for evaluating corrective actions and/or inactions.
The Construction Industry Institute (CII) was founded in 1983 in response to recommendations made by the CICE Project. The second CII task force that was organized was 83-2, Productivity Measurements. This Task Force sought to address many of the recommendations made by the CICE A-1 report. A pilot study was conducted by The Pennsylvania State University to define the more common ways that labor productivity was measured and to determine the feasibility of a standardized approach to productivity measurement. Based on this study, the following definition was adopted:
Productivity – The work-hours required per unit of work. Productivity is the input divided by the output and is calculated for a finite time interval. It is commonly called the unit rate.
A second study was commissioned by the Task Force to develop a standardized approach to measuring construction labor productivity at the task level. This work, which was also done by The Pennsylvania State University, resulted in the preparation of this manual. The manual provides general recommendations and methods based on specific, quantitative data.
The objective of this manual is to describe a task-level labor productivity measurement and performance evaluation system that can be used by owners, contractors, and subcontractors who presently do not have a formalized effort. The procedures are applicable to industrial and commercial projects that exceed several million dollars and to maintenance activities. The emphasis is on inexpensive and accurate measurements that can be made in a timely manner. This is especially important on smaller projects where task durations may last only several months or less. Only selected labor-intensive tasks are monitored, and reporting can be done by a foreman or supervisor.
An earlier finding of the Task Force was that many contractors do not measure labor productivity, and those who do, often do not do so in a way that effectively supports project control. Many reasons are given for not measuring productivity. One of the more commonly cited ones relates to the complexity and cost associated with cost control systems. Many contractors cannot afford the overhead expense inherent with these costing systems. The productivity measurement system described in this manual is independent from a cost control system. It is easy to understand, inexpensive to apply, and accurately reflects what actually occurs on the job site. The system readily accommodates the tailoring of concepts to one’s own special needs. A contractor does not have to alter his mode of operation to fit the system, rather the system should be modified to fit the contractor’s operation. The system can be applied manually or it can be computerized.
The manual provides an introduction to productivity measurement concepts. Basic and advanced techniques are presented. Numerous examples and illustrations are provided so the reader can easily follow how to perform the calculations. Various tables and graphs are given to guide the user in developing clear and concise formats for presenting data.
The experiences of three contractors in applying the techniques are documented. The concepts were found to be readily understood. The flexibility of the system was recognized as a highly desirable attribute. Being able to start with a limited scope of application allowed the contractors to gain confidence with the technique before expanding to more complex activities. The system was readily tailored to each contractor’s mode of operation. The technique was also found to provide timely and accurate results. The system was inexpensive to implement. Examples of data from case studies are given to show how productivity measurement can be used to understand the factors that affect productivity, to monitor and control important activities, and to develop labor units for estimating. The experiences of these contractors illustrates the need to be able to understand the results obtained and to react accordingly.