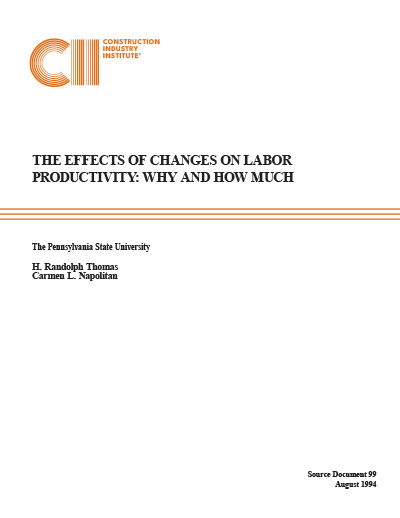
The Effects of Change on Labor Productivity: Why and How Much
Changes and change orders are a source of concern to owners and contractors alike. Changes are an important contributor to cost overruns, schedule extensions, and contract acceleration. This report examines the quantitative effect of changes on labor productivity using productivity data from four active construction sites. In total, the database contains 151 weeks of data and shows a significant average loss of efficiency when performing changes work. Importantly, the report also investigates the reasons why there is a degradation of labor productivity. Understanding the causes is a prerequisite to formulating effective strategies for managing changes.
The report begins with a brief literature review on changes and change orders. It shows that there is little substantive information on the quantitative aspects of changes and that most articles seem directed more toward publicity and advertising. The activities of the Change Impact Task Force to categorize changes is also reviewed.
The analysis of the productivity data reveals that, on average, the efficiency when performing changes work is about 70 percent of normal, that is, there is a 30 percent loss of efficiency. Various statistical analyses are explained that validate this conclusion. The research also reveals that it is possible to perform changes work without loss of efficiency. About a third of the days when changes work was done show no loss of efficiency.
Additional analyses support the conclusion that changes negatively affect labor efficiency. First, it is shown that labor efficiency is negatively affected by disruptions to the work. Next, it is shown that when changes work is performed, there are more disruptions. The percentage of days when disruptions occur increase by about 50 percent when changes occur compared to normal days. The conclusion of this analysis is that disruptions are the proximate cause of loss of efficiency.
The reasons why there is loss of efficiency are investigated by examining the disruption by type. The data reveals that when changes work is performed, there is an increase in disruptions caused by the lack of availability of materials, tools, and equipment. The most significant increase, a four-fold increase, occurs in material deficiencies. There is also an increase in performing out-of-sequence work.
Based on this work, it is concluded that the principal factor leading to disruptions and loss of efficiency is timing. Late changes are particularly detrimental. If changes are identified early, before the work is given to the crafts, the effect of changes is probably minimal. However, if the crew, through their work, identifies the need for a change, then there is an adverse effect of having to stop and wait for information and materials. If the extent of the change cannot be resolved at that point in time, further negative effects will occur. The crew must move to another work location, one for which they may not have planned the work, and returning to the location of the change at some later time may require support services or outage permits. Thus, the early identification of the need for a change is an important element in cost-effective construction.
{^widget|(widget_displayname)WatermarkImage|(name)WatermarkImage|(image)%7e%2fCII%2fmedia%2fPublications%2fSD99_Figure9.PNG%3fext%3d.png|(width)|(height)^}