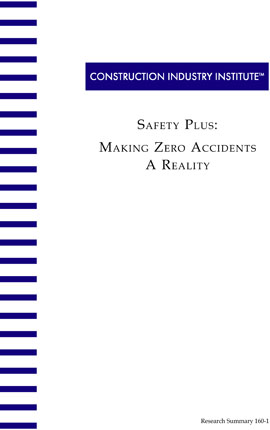
Safety Plus: Making Zero Accidents A Reality
This research effort is a follow-on effort to the zero accidents work sponsored by CII in the early 1990s. Since that time, it has become apparent that changes have occurred in how safety is being addressed by many progressive, proactive construction firms. This study identifies the current best practices in the construction industry that make a difference in safety performance and that move the industry toward the goal of zero accidents.
The Making Zero Accidents A Reality Project Team identified the following nine key topic areas that contribute to improved safety performance:
- Demonstrated management commitment
- Staffing for safety
- Planning: pre-project and pre-task
- Safety education: orientation and specialized training
- Worker involvement
- Evaluation and recognition/reward
- Subcontract management
- Accident/incident investigations
- Drug and alcohol testing
These topic areas, discussed in this research summary, are listed in order of how the development of a safety initiative might take place. There is no attempt to prioritize them. The project team suggests that these initiatives be taken as a consolidated group as good safety performance cannot be achieved with only one of the topic areas being implemented. Of course, it is readily agreed that demonstrated management commitment is of paramount importance.
Key insights on the implementation of these 10 key topic areas are described in RT-160’s research, including: RS160-1 p. 4)
- Demonstrated management commitment must be sincere and conveyed to the worker level.
- Staffing for safety requires full-time safety personnel to ensure safety needs of the project are being satisfied.
- Pre-project and pre-task planning ensures a safety start and that safety is integrated into daily tasks.
- Safety education should include a formal jobsite orientation and additional training focused on the needs of individuals.
- Achieving the goal of zero accidents may be accomplished through behavior observations, worker safety perception surveys, and participation in safety committees.
- Recognition and rewards that are not costly, given often, and based on a specific goal, and that influence worker evaluations that impact wage increases.
- Subcontractor management that drives the safety agenda beyond the general contractor’s own employees.
- Accident investigation that identifies root causes and includes near misses.
- Drug and alcohol testing with random testing.
- Contract type data indicate that cost plus contracts result in better safety performance compared to lump sum contracts.
- Employ full-time safety representatives for fundamental safety tasks instead of using consultants.
- Implement formal safety observation programs on projects.
- Have safety observers on projects.
- Base worker incentives on a specific level of performance, typically below a prescribed injury frequency level.
- Evaluate field supervisors on their safety performance.
- Provide advancement to those with strong safety performance records (proved to be safer) instead of whoever received good ratings or reviews.
- Conduct random drug testing. Safer firms had fewer positive results in their random drug testing.
- Have the company president (in the home office) review project safety reports.
- Provide orientation training for every worker on the project (including subcontractor workers).
- Provide formal orientation training for new hires.
- Give the workers more hours of additional training.
- Involve top management in investigating all recordable injury and lost workday cases.
- Note whether subcontractor safety meetings are held daily.
- Require subcontractors to submit project-specific safety plans.
- Impose sanctions on subcontractors who do not comply with project safety requirements.