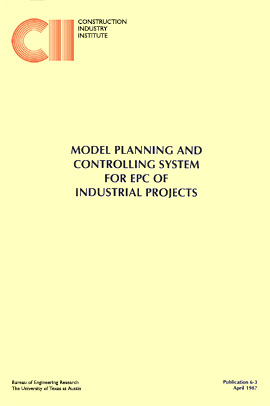
Model Planning and Controlling System for EPC of Industrial Projects
A typical industrial facility is an intricate arrangement of structures, vessels, machinery, piping, electrical systems, and instrumentation packed into a relatively small area. The engineering, procurement, construction, and start-up phases associated with such a facility would be complicated enough if each could be accomplished without dependence on the others. The fact is, however, that they are very interdependent and these dependencies become increasingly critical as the phases are overlapped.
It is impossible to engineer and construct an industrial facility without some overlap of phases. Overlap of engineering and procurement is inevitable in the case of vendor-engineered equipment; some procurement must be handled in parallel with construction to avoid storage space and deterioration in storage problems; and initial start-up testing may have to be accomplished on individual components as they are erected. On the other hand, engineering completion can precede construction and overall start up can await completion of construction. Doing so will increase the design-construct time and owner’s cost, conditions that are seldom acceptable to an owner wanting to get a facility into production. An owner constantly is looking at both time and cost. The time when the facility will be on line producing revenue is of major concern; thus, the shorter the construction time, the better. The owner looks at cost in a different way than does the engineer or constructor. To the owner, life cycle costs are more important than design-construction costs, and these costs are balanced against potential revenues. Lowest design-construction costs are not necessarily the goal. In fact, it may be economically advantageous to the owner to accelerate construction and absorb the costs of such acceleration. It will permit generation of revenues at an earlier time; the earlier revenues totally offsetting the extra construction costs.
To save time, the owner will direct overlap of phases. The question then becomes, “How much overlap and what are the consequences?” Logic tells us that overlap will save time, but that there must be some point at which increased overlapping becomes counter-productive. This is the point where engineering and procurement fail to keep up with construction needs. Rework becomes commonplace and crews are idle. The ultimate result is the addition of time in an amount that totally offsets the apparent time gains of the additional overlap.
Costs may decrease or increase with overlap. While saving time may reduce overhead and time-value of investment costs, all such savings may be overshadowed by the costs associated with rework, idle and demoralized crews, and premium pay associated with acceleration. Again, there must be a break-even point, but not necessarily the same one as for schedule.
Other factors in jeopardy by excessive overlapping are project team relations, workforce morale, quality, and plant operational reliability. The pressures and mistakes associated with extreme fast-tracking can easily strain the relationships among owner, engineer, and contractor and destroy the team atmosphere so essential to success. To the workers, rework and waiting for materials translates into incompetent project management—a major demotivator. In an atmosphere of tension and demoralized workers, quality inevitably suffers.
The approach described in this report is believed to be the one with the optimum overlap—the one which produces a project on schedule, within budget, and of the desired quality. It will shorten time as much as possible while still optimizing costs and preserving quality. The owner’s need date is the ultimate milestone of the process with all contributing activities carefully planned to meet that date. No official claims of time or cost savings are made, although users of the process feel comfortable with time savings in the order of 15 percent compared to the sequential approach, and construction labor savings as high as 30 percent as compared to a fast-track version that permits construction to be initiated on the basis of incomplete designs. The time savings accrue from the planned overlap. The labor savings result from the detailed planning of the project, which reduces project work-hour requirements (early constructability input), minimizes rework (plans & specs available at start of construction), assures materials availability when needed (procurement tracking and materials management), and stimulates productivity (effective project management and a team approach to everything).
Finally, it is appropriate to emphasize again several major thoughts incorporated throughout the description of this system:
- First, the more attention given to a project during its definition, the greater the potential for time and cost savings.
- Second, for the system to work, construction must defer to the needs of start-up, engineering must defer to the needs of procurement and construction, and procurement must defer to the needs of construction.
- Third, there must be a continuous team approach to planning and execution that involves the owner, operator, engineer, procurement group, and constructor.