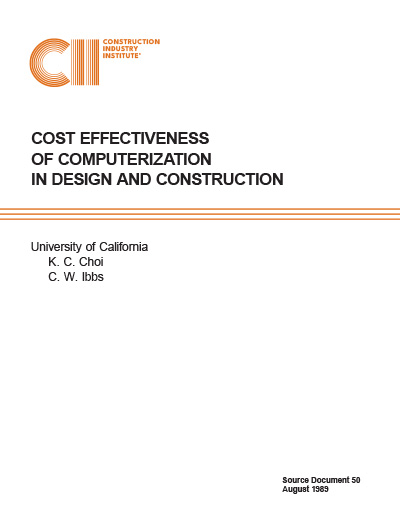
Cost Effectiveness of Computerization in Design and Construction
Computer Aided Design (CAD), Computer Aided Engineering (CAE), and Computer Aided Construction Management (CACM) are playing increasingly important roles in today’s Construction Industry. Their rapid technological changes are dramatically affecting the people and processes in the Construction Industry and the completed facility itself. Many people in the Industry believe that computer technology is and will be one of the most important means for improving Construction Industry cost effectiveness in the foreseeable future.
Although the Construction Industry has accepted the wide use of computers, there is significant concern that adaptation is not progressing in a cost effective and directed manner. In response to this concern, the Design Task Force of the Construction Industry Institute (CII) investigated the cost effectiveness of computerization in the U.S. Construction Industry with researchers at University of California, Berkeley. This report is a product of that investigation. A summary version of this report will be prepared and published by the Design Task Force later this year [Publication 8-1].
Objective
The primary study goal is to collect and share lessons learned about recent computerization efforts among CII companies. Findings presented in this report will assist the entire Industry in using computers more cost effectively and avoiding some of the costly mistakes of the past. Through this report, senior management in the Construction Industry can learn the present status of computerization and the trends for the next three to five years. This report also identifies the areas that need Industry-wide attention to improve the value of computerization.
Based on the broad objectives addressed above, the following specific study goals were established for this research:
- Capture information about the current status and recent trends of computer usage in the Construction Industry.
- Evaluate and analyze cost effectiveness of CAD/CAE/CACM.
- Investigate ways for each company to estimate its own computerization cost effectiveness.
- Identify important factors, problems, and needs for cost effective computerization.
- Summarize future trends and predicted cost effectiveness for the next three to five years.
- Identify areas of needed additional research.
Methodology
Information required for this study was collected in four phases:
- Questionnaire survey.
- Follow-up site interviews with selected CII firms and software vendors.
- A series of meetings with CII Design Task Force subcommittee members.
- A two-day Workshop with Industry experts.
Though the study findings presented in this report are based on the data collected mainly from the CII member companies and inputs from CII “Resource People,” they should be useful to a wide audience throughout the Industry.
Present Status and Future Trends of Computerization
Computer applications in the Construction Industry can be categorized into five major areas:
- Administration and accounting programs: typically mini- or mainframe based.
- Minor, non-graphic engineering and project management applications: typically microcomputer based.
- Major, non-graphic engineering and project management applications: typically mini- or mainframe based.
- 2-D CAD systems: typically micro- or minicomputer based.
- 3-D CAD systems: typically mini- or mainframe based.
All applications, except 3-D CAD systems, are widely used and accepted with varying degrees of sophistication in the Industry. Few people question their cost effectiveness. Benefits are measurable in such terms as better design with improved productivity, lower home office costs, and shorter design schedules.
The Industry is now unevenly moving into application of 3-D modeling systems. These spatial management systems cost more in terms of hardware, software and training. Home office benefits from these 3-D systems are not as apparent as for the 2-D and previous systems. However, the Workshop participants believe that the higher-powered systems do reduce total project costs enough at this time to justify the investment on a much wider industry basis. The major impediment is the size of the investment; e.g., $25,000 to over $100,000 per seat. This is particularly acute when the design and construction functions are performed by separate companies, and the design organization has no direct share in the field cost savings. Owners really are the principal beneficiaries of 3-D CAD systems. Owners have begun to demand and use electronic design databases prepared by engineering contractors at a rapid pace to support on-going facility management.
We observed that large engineering and EPC firms are computerizing aggressively to just to stay abreast in a highly competitive market. On the other hand construction only firms seem to be computerizing more cautiously with the result of increases flowing down to their profit lines. A detailed account of this assertion is in Chapter 6.
Computerization of engineering work has been analyzed in detail in this study. To summarize, the Industry is presently completing computerization of manual processes in engineering, especially in the graphics world. The questionnaire survey shows that slightly less than 50% of all engineering tasks are done using computers. It also shows that design and drafting functions, one of the three major engineering tasks defined in this study, will be computerized at the fastest rate in next three to five years, from a present 53% to 88%. Computerization of numerical analysis functions and "other" engineering tasks will continue, but at slower rates.
The Industry will depend more on software vendors than internal resources for software development in the future. Object oriented database-driven CAD/CAE systems will become popular in the next three to five years. Increasing use of expert systems, other artificial intelligence concepts, and dynamic walk-through simulation programs is anticipated. Simulation of the conceptual design of projects will be among the engineer constructors capabilities.
Bar-code technology is gaining popularity for materials management in the Industry. Many companies have already convinced themselves that this technology is cost effective in field materials control, and are using them regularly. Materials and small tools are identified by unique identification numbers and managed effectively in a computer integrated environment. Use of Industry-standard product codes will make this system more cost effective.
In three to five years most engineers will have a computer on their desk and use it a substantial part of the time. Increasing use of high-end supermicro and low-end minicomputers, called technical or engineering workstations, is anticipated. These computers will be much more powerful than current models. Heterogeneous hardware platforms tied to local area networks (LAN’s) and wide area networks (WAN’s) will be the choice for the future. “Ethernet” seems to be the choice here. LAN’s and WAN’s will link all kinds of machines for communication. Achieving maximum flexibility and compatibility between hardware and software will be a strategic focus for cost effective computerization. Due to the demand for open software systems that can be run on wide range of hardware platforms, bundling of hardware and software will be even less favored in the future. Increasing use of UNIX operating system is anticipated due to its power and portability.
Industries will develop unique project and company databases. Owners and contractors both will draw information from their own company databases and industry databases, and create from them project databases to be used for construction and other business requirements. Computerization is moving at a pace that leaves today’s tools and methodology obsolete at an alarming rate. The next five years are viewed as exciting and expensive times for the Construction Industry. Poor planning will make those years even more expensive.