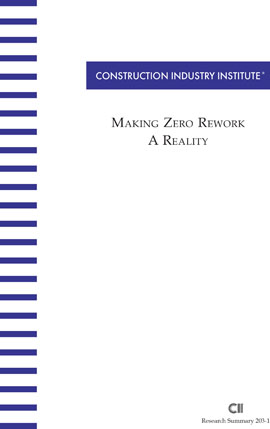
Making Zero Rework A Reality
The construction industry, led by CII members, has made great strides in improving its safety record over the last decade. The same cannot be said, however, regarding rework. Many industry participants have been claiming that rework, and “doing it right the first time,” are priorities, but the increasing rework activity on projects both large and small belies this claim.
The Construction Industry Institute formed the Do It Right the First Time Research Team to investigate field rework and find ways to improve this costly activity. The primary purpose of the research was to identify and describe the primary components of a comprehensive process for management and elimination of quality-error related costs for construction sites. While many errors and omissions occur in the scope development process and design, the focus of this project was limited to implementation of error-reduction activities on the project execution level and within the construction organization.
The research team first looked at methods and techniques that have been effective in implementing safety management and in reducing accidents and lost workdays in construction. It found that management support and pre-project tasks were consistent for both safety and quality activities. The difference occurs in the implementation level between planning and field execution. Most importantly, the research found that worker involvement is needed to resolve the continuing problem of rework. Specifically, the research team found that increasing training on quality issues, identifying quality rework problem areas, increasing fulltime quality staff, and having field personnel analyze pre-task quality efforts all contribute to less rework.
Taking a cue from the CII research on safety, the research team now is urging the industry to take a similar look at rework. In addition to zero accidents, the industry needs an attitude of “making zero rework a reality.” If it does, the resulting low percentages of rework could pay for error reduction efforts.
Management commitment for rework reduction was found in the research. Management support and pre-project tasks were consistent for both safety and quality activities.
If management is committed to rework reduction by putting time and resources into an effective system, then rework direct and indirect will decrease. The management system to be effective must involve the buy-in of management and employees who share in the benefits of the successful system.
Generally the respondents provided more consistent data for commitment to safety than for rework or quality management. However, the overall commitment was not sufficiently different to suggest that management is not committed to effective processes. Qualification processes or techniques were generally lacking consistency; however the reporting, management accountability, and goal setting were clearly supported in the data.
The inclusion of quality personnel at project management meetings would also be a reflection of management commitment to the quality function on the project.Staffing levels for quality were generally lower than safety, given the requirement of discipline specific knowledge for quality. No correlation was found for project size and staffing levels for either safety or quality.
Inspection personnel in quality acceptance should have some form of certification to perform their project function.Pre-project planning, constructability analysis, and project specific quality plans were consistent with safety planning. Pre-mobilization quality analysis and pre-task quality analysis were lagging.
(RS203-1, p. 25)
Is there evidence of pre-project and pre-task planning targeting rework reduction? The data shows an area for improvement exists in performing quality analysis of the project prior to mobilization and engaging field personnel in quality pre-task planning activities.
Site-specific pre-task quality planning, job quality analysis, and constructability reviews were included in the survey. These elements are key to describing what project level personnel are responsible for in the quality management planning for the project.Safety education is averaging 3 hours per month compared to quality training at 0.5 hours per month. A standard quality orientation was implemented on less than half of the projects. (RS203-1, p. 25)
Increasing training on quality issues, identifying quality rework problem areas, increasing full-time quality staff, and having field personnel analyze pre-task quality efforts all contribute to less rework. Is there formal training directed toward reducing rework on projects?
There is room to improve in the area of education on quality related issues. Training is clearly an area where there is disparity between safety and quality systems. Rework reduction would likely benefit from worker orientation to quality processes on the project and specialized training when appropriate.Subcontractors are often required to use the prime contractor safety plan. Some projects require that the subcontractor submit their own safety plan for the project. Quality planning should follow a similar pattern. Subcontractors are more commonly required to submit safety plans than quality plans. (RS203-1, p. 9)
What provisions are made to manage subcontractor rework or quality? Prequalification of subcontractors for safety and quality had similar responses and appear to be a common practice.Lump sum contracts were shown to have less rework than reimbursable contracts which is opposite the relationship for safety. (RS203-1, p. 25)
The type of contract could easily influence the quality program effectiveness if additional expenditures on quality would be perceived as cutting into profits.