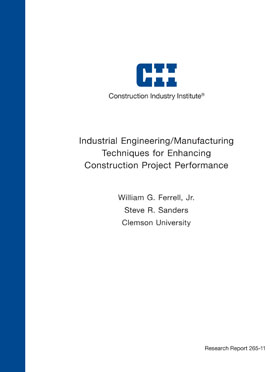
Industrial Engineering/Manufacturing Techniques for Enhancing Construction Project Performance
Previous CII research suggests that field project operations are quite inefficient. For example, the final report of Research Team (RT) 191 indicates that "NVA (non-value adding) activities consume between 50 and 75% of the productive time on the jobs." While some might have a legitimate quibble over the exact numbers on productivity, it is hard to justify anything close to a 1:1 ratio as an acceptable description of productive to nonproductive time in any business. So even if we only agree that NVA activity is unacceptably high, companies capable of steadily reducing it in field project operations could parlay this into a strategic advantage and a source of increased profits. The question for companies who want to reduce NVA activity, then, must be “How?“ because if they knew this answer, progress would most certainly have already been made. This is the context within which RT265 interpreted our fundamental question – identify techniques and practices from industrial engineering (IE) and manufacturing that could be used to reduce NVA activity in field project operations.
A significant hurdle faced by the RT and one that will be faced by anyone wishing to implement these finding is that there are very few industrial engineers in construction. This means that there are few IE techniques currently implemented in field project operations to use as examples. It also means that there are few people who can discuss the potential benefits of implementing IE techniques to skeptics. The problem is compounded by the fact that there seems to be a commonly held but inaccurate view of IE, believing the techniques are only applicable to “repetitive manufacturing“ so they cannot work in “one off“ construction projects. The Institute of Industrial Engineers is the worldwide professional society for IE and defines the discipline as being “concerned with the design, improvement and installation of integrated systems of people, materials, information, equipment, and energy. It draws upon specialized knowledge and skill in the mathematical, physical, and social sciences together with the principles and methods of engineering analysis and design, to specify, predict, and evaluate the results to be obtained from such systems.“ Less formally, IE is known in many circles as a discipline that focuses on improving efficiency and effectiveness by taking a holistic systems and process approach to problems. The techniques that are the fabric of IE practice have been implemented in a wide variety of application domains to eliminate wastes of time, money, materials, energy, and other resources with tremendous success. The application domains include health care, finance, tourism, retail, distribution, shipbuilding, and aircraft construction just to name a few. Clearly, these have little in common with repetitive manufacturing and many have underlying dynamics much closer to construction than manufacturing. As such, successfully implementing the results of this research in field project operations to claim the significant benefits they produce will require strong leadership to overcome the well-intentioned but misguided skepticism.
To provide construction site personnel with the information required to successfully implement IE techniques and reduce NVA activity, the RT adopted three primary objectives:
- Develop a tool that will allow construction site personnel to identify “waste“ (i.e., NVA activity in the language of “lean“) in site processes that can be improved by application of IE techniques and then to identify the IE techniques that can be used in these situations.
- Develop a tool that will allow construction site personnel with no experience or in-depth knowledge of IE to successfully implement the IE techniques identified in objective #1 so that waste is eliminated and so that the resulting benefits are sustained.
- Ensure that the interface between these tools and the end users is designed and built to their specifications including but not limited to format, structure, and language. The intended end users of these tools are superintendents, foremen, warehousemen, and other individuals responsible for planning the execution of construction projects.
Identifying a methodology to achieve these objectives was difficult since the team believed that there was a general lack of familiarity with IE techniques in the construction industry so using field data was not an option. After much deliberation, the RT selected an alternative approach that parallels engineering design. Rather than collecting data and using statistics to draw valid inferences, this approach matches the fundamental causes of problems in the field with IE solutions designed to address these causes so successful applications of the IE techniques are guaranteed. This approach has several steps: 1) identify sources of waste from problems encountered on the site, 2) decompose each problem until the root cause is exposed, and 3) match IE techniques to the problem based on the theoretical underpinning of the techniques and the root causes of the problems. The results are interesting, rigorous, and extremely useful. Applying this research methodology produced three primary tools.
- Problem Identification Flowchart – This tool is a decision tree that leads site personnel from general problems to elemental problems and, then, to applicable IE techniques by asking a series of simple questions.
- Planning Assistant – This tool parallels the first but focuses on applying IE techniques during the planning phase that can prevent problems later in the project. This tool is not, and is not intended to be, a comprehensive guide to planning; rather, it is developed to focus on specific activities undertaken during planning that, if done better, would avoid problems later. Some of the planning functions discussed are: site design, laydown area design, warehouse design and operations, work area design, and work station design.
- Input Management – This tool provides knowledge to a user that, if understood and adopted, creates a lens through which planning activities and daily problems can be viewed that will allow IE techniques to be successfully applied within the scope of this research and beyond.
Finally, all of the IE techniques that were found to be useful in the three tools noted above were adapted to field project operations and made usable for the target audience with step by step implementation procedures. Additional information and references are also included for each.
These tools are applicable on all construction . . . all. That is not to say that every IE technique or every planning tool is applicable in every situation because they are not; however, the RT is completely convinced that every single construction project would eliminate some waste and reduce NVA activity to some degree by using these tools. It might be a warehouse manager who better controls inventory of key consumables using the fundamentals of order point/reorder quantity so that craft labor never run out of parts, they are easily found because clutter is reduced, and excess inventory is not held. Or it might be the laydown area that is designed using concepts of Systematic Layout Planning that allows a critical component to be located and delivered to the work face quickly, without anyone searching for it or being forced to wait for a crane with a longer boom because other materials had been placed in front of it. Or it might be that a planner understands that a new problem being encountered is just an inefficient way of buffering variability and uses the input management tool to find an alternative way that is better for the project schedule and financial performance. The point is that the RT cannot predict the precise pathways that might help a specific project or even how many pathways will be helpful on any given project; however, we are convinced that using these tools will produce wins on the job site which will encourage more widespread use of the tools and even more wins. Give them a try and see for yourself!
RR265-11, Problem Identification Flowchart
Each flowchart is a decision tree that leads site personnel from problem identification to IE techniques that might improve the situation. There is a flowchart for each of the 5 NVA categories: (RR265-11, p. 31)
- Equipment
- Materials
- Tools
- Information
- Personnel
This tool addresses the use of IE techniques during the planning phase that can prevent problems later. The purpose of the Planning Assistant is to provide the project team with a systematic approach (step-by-step instructions) for planning the layout of a construction site. (RR265-11, p. 55)