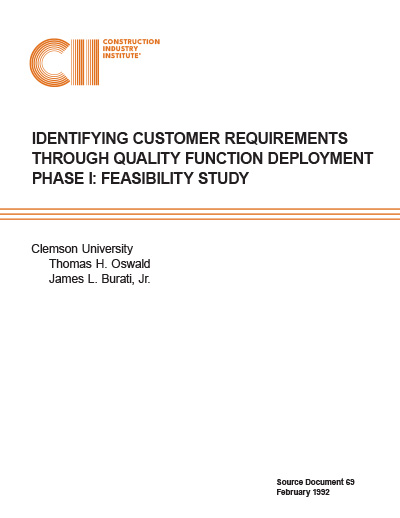
Identifying Customer Requirements Through Quality Function Deployment
Quality Function Deployment (QFD) is a planning and communication tool of proven value in manufacturing and service industries, in the design of new products and services and the improvement of existing ones. Appendix A contains more complete descriptive information on QFD.
This research was commissioned by the Construction Industry Institute (CII) to determine the feasibility of adapting QFD for use in the project management process of the engineering and construction (E&C) industry. The findings are clear:
- Quality Function Deployment has definite value as a tool for improving the project definition process.
- It has step-change potential for use by both Owners and Contractors.
- The benefits are concentrated in the areas:
- Enhanced identification of, and response to, customer requirements.
- More complete up-front planning.
- Reduced cycle time, through less redesign.
- Better cross-functional communication.
The Engineering and Construction Challenge
Project definition—the “scope problem”—is generally cited by engineering and construction (E&C) practitioners as the single, greatest source of poor efficiency in the overall interaction between owner and contractor, as measured by false starts, rework, disputes, claims, and litigation. There is no commonly accepted method used in the industry.
One of the conclusions of the Business Roundtable’s Construction Industry Cost Effectiveness (CICE) Study (2) was that:
“Poor scope definition at the estimate (budget) stage and loss of control of project scope rank as the most frequent contributing factors to cost overruns.” |
Succeeding research by the Construction Industry Institute (CII) found that
“... when there is poor scope definition, final project costs can be expected to be higher because of the inevitable changes which disrupt project rhythm, cause rework, increase project time, and lower the productivity and morale of the work force.” |
QFD’s Strengths
This research produced observations about the results of using QFD, which can easily be related to the project definition problem:
- A highly effective planning tool.
- Significant payoff when used to achieve breakthrough changes in areas or deficient or critical customer satisfaction.
- A method for more precisely defining the “it” in “Do it right the first time.” Produces a more rational set of design decisions, and highlights potential conflicts early in the design process.
- A structured approach to handling critical and complex sets of requirements.
- Reduction of cycle time through reducing redesign and improving inter-functional communication.
- Effectiveness in breaking down barriers among people and organizations.
How Owners Would Benefit
Owners generate projects and benefit from the accomplishment of project objectives. They therefore have the ultimate stake in finding improved methods for project planning. Potential planning benefits which might accrue from the use of QFD include:
- Optimum internal definition of project requirements, coordinating such diverse considerations as market timing and financial, technical, production, and maintenance inputs.
- More efficient communication of the requirements to the design/construction contractor(s).
- Shorter cycle time from project concept to startup.
- Greater conformance of project execution to project requirements.
How Contractors Would Benefit
Although the owner bears the final brunt of inefficiencies in project planning and execution, the E&C contractor experiences severe disruption to its own business stability when such problems occur. The contractor should experience the following benefits from using QFD, in conjunction with a knowledgeable owner:
- A standard approach to obtaining and using the owner’s requirements.
- A more complete set of owner requirements, and a more complete understanding of them.
- Fewer conflicts in design requirements.
- Less rework, leading to lower costs and shorter project execution time.
- Greater opportunity to integrate constructability concepts into the design.
What Is Lacking for E&C Implementation of QFD
QFD is a relatively new tool in the set of methods available to U.S. companies for improving quality and productivity. It has not been widely used in the E&C industry, and therefore there exists no widely understood “application framework” by which firms can understand the technique and how it might be applied in the project management process.
Recommendations
The TQM Task Force recommends that the Construction Industry Institute fund a follow-up project to define an application framework for implementing QFD in the E&C industry, incorporating the following main features:
- A focus on application of QFD in the project definition phase.
- A practical, working model of the QFD technique, developed with the assistance of two owners and two contractors, preferably CII member companies who have some QFD experience or knowledge. Details of the model are outlined below.
- Application guidelines for owners’ and contractors’ internal use, as well as for joint owner/contractor use.
- Guidelines for Integrating QFD with current methods of project definition, where such would be constructive.
The E&C application framework, or working model, would define the following:
- How to set up the QFD project, including fitting it to an appropriate E&C project and scoping the QFD effort.
- How to form the QFD team, including team composition, chartering, training, facilitation, and logistics.
- How to structure the QFD graphic aids (the “House of Quality” and other matrices).
- The requirements for pre-QFD setup and “homework” to be accomplished by each party, owner and contractor.
- How to organize the initial input, the owner’s requirements and the contractor’s technical capability, for most efficient QFD processing.
- How to conduct team meetings: objectives, agendas, team assignments, follow-up tasks, etc.
- How to complete and interpret the QFD matrices.
- How to use the QFD output over the remaining life of the project.
- How to provide for ongoing QFD process ownership and facilitation.
The Phase II project could be completed by early 1993, assuming approval and contract execution by June 1, 1992. Preliminary work on the model would proceed during the period January–May 1992, independent of CII funding. The CII-funded portion would carry this preliminary development to at least two CII owners and two CII contractors for detailed development and evaluation by the individual companies, and finally in a workshop setting attended by all the participating companies. The preliminary and detailed design of the model would be accomplished via limited-scope, low-risk pilot applications in the participating firms. Such would produce “real time” development and feedback, thus maximizing the Phase II output and making it ready for use by interested companies in a comparatively short time period.
A Phase II project proposal to CII accompanies this report.