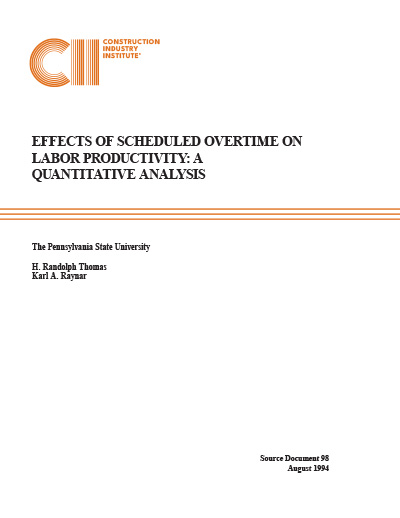
Effects of Scheduled Overtime on Labor Productivity: A Quantitative Analysis
Scheduled overtime has been a controversial subject since the mid-1960s. In the early 1970s, The Business Roundtable (BRT) published a report on the effects of scheduled overtime. The BRT report added to the controversy. The purpose of this report is to present the quantitative results of a study into the effects on labor productivity of scheduled overtime. This report is the most comprehensive study of overtime since the BRT report. It is based on 121 weeks of data from four active industrial construction projects. Major contract disputes were not involved in any project, and the labor environment was good. Both union and merit shop labor forces were included in the study. This report is a companion report to an earlier Construction Industry Institute report that surveyed the literature on scheduled overtime (Thomas et al. 1990 [SD-60]).
The initial investigation of overtime is the effect of the number of days worked per week on labor efficiency. Work weeks of 5 and 6 days show losses of efficiency of 12 and 14 percent, respectively. Next, the data is examined for the efficiency trend of working multiple weeks of overtime. The analysis shows that about 25 percent of the time efficiency is not impaired for durations of 2 to 4 weeks. However, on average, there is a likelihood of productivity degradation, even for 1- to 2-week periods. An average curve is calculated and compared to four curves from the literature showing efficiency versus multiple weeks of overtime. The results show that all curves, including the data from this study, are consistent. The conclusion is that the BRT curve is a reasonable average estimate of productivity losses caused by overtime. Since none of the projects in this study are severely impacted with schedule or labor problems, these curves likely represent a lower limit of the losses that can be anticipated. Poorly managed or executed projects will likely experience greater losses.
Efficiency losses are further investigated by examining the influence of disruptions. A normalized disruption frequency is calculated, and it is shown that as the disruption frequency increases, the efficiency decreases. This analysis establishes a causal relationship between disruptions and efficiency losses. Three disruption categories are defined. Management and rework disruptions show mixed results. That is, there is no clearly established relationship between the disruption frequency and the number of days worked per week. Resource disruptions are defined as the lack of materials, tools, equipment, or information. The frequency of resource disruptions increases sharply for longer workweeks. For the 6-day workweek (60 hours per week), there is almost a three-fold increase in the resource disruption frequency compared to the 4-day workweek (40 hours per week). The conclusion is that working overtime efficiently is a resource management problem.