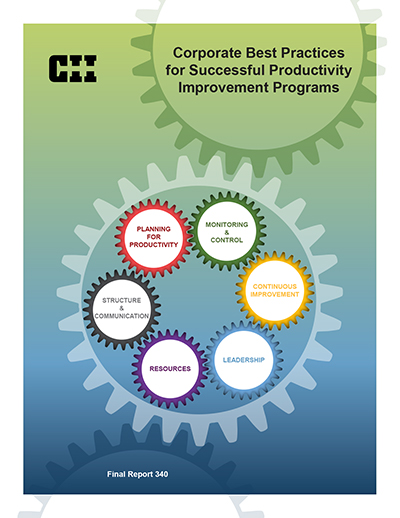
Corporate Best Practices for Successful Productivity Improvement Programs
In the construction industry, productivity improvement is a critical aspect of successful project planning and execution. Specific productivity practices have demonstrated improvements at the activity, trade, and project levels; however, results have been inconsistent and the productivity gains have not been significant at the corporate and industry levels. This research by CII Research Team 340, Corporate Practices for Successful Productivity Improvement Programs (RT-340), studies the productivity improvement challenge from a corporate perspective, which influences entire project portfolios. The objective is to characterize and assess Corporate Productivity Programs, which are comprised of the people, processes, and technologies that support an organization’s productivity improvement efforts. To this end, the Construction Industry Institute developed the essential research question investigated through this research, “What are the enterprise-level best practices for implementing productivity improvement programs; and what are the most significant barriers to their implementation?”.
In pursuit of effective corporate-level programs to generate portfolio-wide impact, the research team leveraged existing programs in safety and lessons learned to understand roles, responsibilities, practices, barriers, and interfaces common among these established corporate programs. That basis gave support for a familiar program structure, like the measurable actions and tenets for success.
In identifying the best corporate practices and barriers for the successful implementation of productivity improvement programs, 94 Actions and 60 Barriers were identified based on literature review, interviews with subject matter experts, and research team analyses. Actions are defined as measurable enterprise-level best practices of Corporate Productivity Programs that enable successful program management and implementation of proven productivity practices across company project portfolios. These Actions span many aspects of company business, such as, development of goals and objectives to focus company efforts, performance of project controls processes, and utilizing metrics for continuous improvement. The research team categorized these 94 Actions in six key Elements:
- Leadership
- Resources
- Structure and Communications
- Planning for Productivity
- Productivity Monitoring and Control
- Continuous Improvement.
Executive engagement is critical to successful implementation of RT-340 findings. Because the Corporate Productivity Program seeks to improve organizations’ full project portfolio, sponsors need authority and long-term commitment to drive improvement. With that influence, a company’s Corporate Productivity Program is able to leverage the RT-340 findings. This begins with defining the program’s roles and responsibilities, which are then assessed.
This structured program Implementation Framework enables corporate leaders to focus efforts and resources on key areas and specific company issues. Through identification of strong and weak program Actions, program sponsors can guide the improvement path and responsibilities. Additionally, identifying and recognizing likely Barriers enable mitigation of potential pitfalls specific to the company’s program. These assessment processes enable implementation planning with program participants aligned on specific Actions, Barriers, and objectives that span across the corporate and project organizations.
Through improving the Corporate Productivity Program, a company should have increased utilization and consistency with implementation of proven productivity practices. Successful systematic implementation of these proven productivity practices can generate more reliable management of productivity efforts across project portfolios. These systemic productivity improvements have the potential to increase performance and predictability for portfolio management in the multi-trillion-dollar construction industry.
Data were gathered to assess sources of the inconsistent implementation across company portfolios. The lack of corporate ownership contributes to the challenges of consistent productivity practice use and implementation.
Barriers exist across organization groups and departments as well as vertically in company hierarchies. This research identified key and common themes inhibiting success and aides companies with identification of program-specific Barriers.
The Implementation Framework of the Corporate Productivity Program is designed to enable a company to identify program strengths and weaknesses. These strengths and weaknesses consist of evaluated Actions that represent program-level best practices. In addition, likely barriers to program success are identified through relationships with weak Actions.