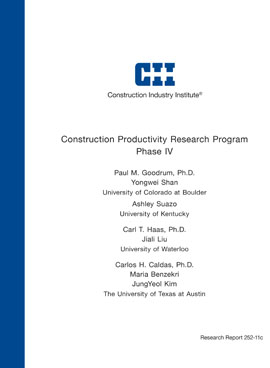
Construction Productivity Research Program -- Phase IV
Achieving a 50% improvement in construction productivity in six years would break a century old tradition of stagnation, interrupted by periodic productivity improvement. The first three phase of a six year research program was successfully completed. The following report details the findings from the fourth phase of the Construction Productivity Program with a focus on steel trades.
Direct work typically amounts to no more than 35-45% of a craftsman’s time on the job. To improve craft productivity, direct work time must be improved. To increase direct work time, the availability of materials, information and tools at the workface must be improved. There is no “magic bullet” to make this happen, but rather a series of innovations that together produce a significant productivity change in construction. Since the program’s inception, the innovations include a combination of broad improvements in practice and focused improvements in technology and process.
To achieve improvements in construction productivity as measured by direct work, unit rates of labor productivity, and rework, Research Team 252’s (RT 252’s) rolling, five phase program injects innovations annually via a sequence of innovation workshops, field trials, analysis, and implementation tool delivery. Each phase of the program involves: (1) analyses of the CII BM&M data to identify best practices that appear to have an impact on productivity, (2) exploring opportunities for productivity improvement through craft information, technology support for labor, work packaging/organization, and human behavior, and (3) soliciting innovation input from structured workshops and team members’ expertise.
Analysis of BM&M data in the fourth phase was focused on investigating the relationship between project management programs and productivity of the steel trades. Significant relationships were found between improved productivity and best practices in front end planning, automation of information systems, materials management, constructability, and safety. These practices, however, are not additive; there are synergies between these practices. Projects that were advanced implementers of these practices experienced at least 32% average productivity advantage over projects that were weak implementers. Clearly, implementing these best productivity practices can make all the difference between a weak and a strong performer.
RT 252’s efforts in the first research phase also focused on a thorough search and definition of best productivity practices. Thus far, these practices have been rigorously weighted and properly structured and become part of a Best Productivity Practices Implementation Index (BPPII). Through field validation, it has proven that the BPPII is a rigorous tool that will help improve construction productivity. In the final phase of this research program, BPPII will be delivered as an implementation tool. No existing CII tool addresses productivity as directly as the BPPII will.
For this phase of the program with its focus on steel construction, steel quick connection systems (SQCS) were identified and compared with conventional steel connection systems, and the potential benefits in terms of construction productivity and costs were further investigated through field observation and data collection. The team outlined the applicable area of the innovation and described the difference of the innovation with other similar technologies. Then, the process of design and construction were compared between conventional steel connections and SQCS. Next, cost and labor productivity analyses was performed on 9 projects. Furthermore, activity analyses were performed on two ongoing case projects. Finally, the productivity gain as a result of using SQCS were visualized through 4D schedule simulation with the assistance of building information modeling technology.
Implementing the best productivity practices identified in this forth phase is expected to result in significant productivity improvement on your project. More is yet to come in the last project phase. This report includes five chapters. Chapter 1 introduces the research effort as a whole and for this phase. Chapter 2 analyzes project practices and productivity relating to the steel trades. Chapter 3 investigates SQCS and its potential benefits. Chapter 4 introduces the structure, scoring mechanism and validation of the contractors’ workforce develop assessment (CWDA) tool. Chapter 5 takes a holistic view of the BPPII development from inception to the validation. Chapter 6 is the conclusions of this report.