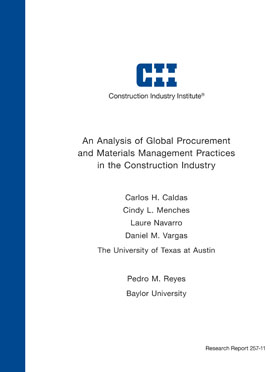
An Analysis of Global Procurement and Materials Management Practices in the Construction Industry
Globalization is a well-established but complex trend. The globalization of owner materials standards, standard processes, and preferred suppliers will continue to increase as the trend becomes more pervasive. In addition, quality concerns may trigger the further development of processes to help determine when local sourcing is preferable to global sourcing.
Sourcing from emerging markets is not as widespread as one might imagine; only 35% of respondents report having significant involvement in this type of sourcing—with more contractors than owners saying that they do.
Figure 18 (RR257-11, p. 138)
Globalization has enabled entities to source materials worldwide. Emerging markets now interest organizations willing to take advantage of low-cost country sourcing. However, the extra costs of expediting, supplier quality management, transportation and logistics, and customs clearance efforts can sometimes compromise these suppliers’ cost-effectiveness.
Sustainability is a new major topic at the top management level. Eighty-two percent of respondents declare their organization to be significantly concerned with those issues. Seventy-four percent have sustainability objectives as an explicit part of their organizations’ strategic plans.
Seventy four percent of the survey responses said that materials management was a part of their corporate strategic plan. According to 63% of the respondents, the use of strategic supplier relationships was part of the corporate strategy. Seventy-six percent of the companies surveyed used sourcing agreements—e.g., master agreements—at the corporate level.
Table 52 (RR257-11, p. 54)
The survey results also showed that the materials management groups were involved earlier in project planning than they used to be. (RS257-1, p. 6) Early project planning should include global market studies that not only identify the least expensive sources of equipment and materials of verifiable quality, but that also consider the costs and complexity of global logistics in more detail than has been customary up until now. (RS257-1, p. 32)
A great majority of the contractors surveyed acknowledged that they were experiencing scheduling challenges due to competing demands upon the subcontractors’ capacity, prompting an increase in the use of modularization. Surprisingly, in spite of constraints on available supplier capacity at the time of the survey, few organizations were purchasing lock-in of shop manufacturing capacity in advance. In addition, most organizations have experienced an increase in late deliveries and were thus increasing the amount of expediting for second and third-tier suppliers. Both types of organizations tend to use third-party providers for expediting, in-shop quality surveillance, and transactional shipping support.
The majority of organizations surveyed appeared to have a sophisticated supplier quality management system that includes: inspection plans, supplier quality evaluation before selection, supplier databases, design quality reviews, and materials management process audits. Organizations also seem to do a good job at qualifying, evaluating, and monitoring suppliers and subcontractors. Forty-seven percent of respondents also reported that their organizations faced instances of non-conformance and defects more frequently. Documented quality processes and performance will become increasingly important factors in the early stages of developing the Project Acquisition Strategy (PAS).
Table 72 (RR257-11, p. 61)
Seventy-one percent of the organizations surveyed acknowledged that they have an integrated materials management computer system, usually using a combination of commercial software, custom-made software, and/or an enterprise resource planning (ERP) system.
The refinement and standardization of interfacing among IT systems offers great potential for improvement. Materials managers should influence IT systems selection and their integration during pre-project planning. Training programs should be better integrated into project schedules so that employees’ use of materials management IT systems is continuously improving.
Table 41 (RR257-11, p. 44)